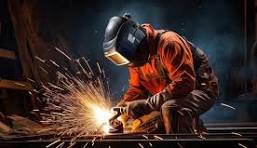
As a beginner in the world of welding, selecting the right welding rod can be a daunting task. With numerous types of welding rods available, each with its unique characteristics, applications, and benefits, it’s essential to understand the basics of welding rods to make an informed decision.
Understanding Welding Rods
Welding rods, also known as electrodes, are an essential component of the welding process. They are made from metal and coated with a flux that helps to protect the weld from contamination and oxidation. The welding rod is used to create an arc between the welding machine and the metal being welded, which melts the metal, and the molten metal then cools and solidifies to form the weld.
Factors to Consider When Choosing a Welding Rod
When selecting a welding rod, there are several factors to consider, including
The type of metal being welded
Different metals require different types of welding rods. For instance, if you’re welding mild steel, you should use an E6013 or 7018 welding rod. If you’re welding stainless steel, you should use an E308L welding rod.
The welding position
Some welding rods are designed for use in specific positions, such as overhead or vertical welding. Using the wrong rod for the position can result in a poor quality weld.
The desired weld properties
Different welding rods produce different weld properties, such as penetration, strength, and appearance. Choosing the right rod for the desired weld properties is crucial.
The skill level of the welder
As a beginner, you may want to choose a welding rod that is easy to use and forgiving. More experienced welders may prefer rods that require more skill and precision.
Common Types of Welding Rods and Their Applications
Welding rods are classified based on their properties and are assigned an alphanumeric code. This code is one or two letters followed by four or five numbers, and each has a specific meaning. Here are some of the most common types of welding rods and their applications:
6010 Welding Rods
Application: All-position welding, ideal for welding in tight spaces
Properties: Deep penetration, excellent arc stability
Uses: Construction of pipelines and pressure vessels, general fabrication
6011 Welding Rods
Application: All-position welding, ideal for welding on thin materials
Properties: Versatile, suitable for use on both AC and DC welding machines
Uses: General fabrication, automotive repair
7018 Welding Rods
Application: Low-hydrogen electrode, ideal for welding carbon and low-alloy steels
Properties: Produces a strong, high-quality weld
Uses: Welding structures, such as bridges, buildings, and pipelines, heavy equipment, such as cranes and bulldozers
How to Choose the Right Welding Rod for Mild Steel
When it comes to welding mild steel, there are several factors to consider before selecting the right welding rod.
These include: The thickness of the metal: Thicker metals require larger-diameter rods, while thinner metals require smaller-diameter rods.
The welding position: Some rods are designed for use in specific positions, such as overhead or vertical welding.
The type of joint: Different rods are better suited for different types of joints, such as butt joints or fillet welds.
Best Welding Rods for Cast Iron and Other Metals
When welding cast iron, a 312 or 316 rod is recommended. For aluminum, an ER4043 or ER5356 rod is ideal. For stainless steel, a E308LT-1 or E309LT-1 rod is recommended.
Common Mistakes to Avoid
When selecting a welding rod, there are several common mistakes to avoid, including:
Not Considering the Base Metal
Using a welding rod that is not compatible with the base metal can result in a weak or brittle weld.
Not Considering the Welding Position
Using a rod that is not designed for the specific welding position can result in a poor quality weld.
Ignoring the Material Compatibility
Using a welding rod that is not compatible with the base metal can result in a weak or brittle weld.
Failing to Store the Rods Properly
Improper storage of welding rods can result in poor-quality welds. Always store your welding rods in a dry place to prevent moisture from getting into the flux coating.
Conclusion
Choosing the right welding rod is essential for a strong and lasting weld. By considering the type of metal being welded, the welding position, the desired weld properties, and the skill level of the welder, you can make an informed decision and select the right rod for your project. Remember to avoid common mistakes, such as not considering the base metal, not considering the welding position, ignoring material compatibility, and failing to store the rods properly. With the right welding rod, you can achieve high-quality welds and complete your projects with confidence.
Read More (Click Here)