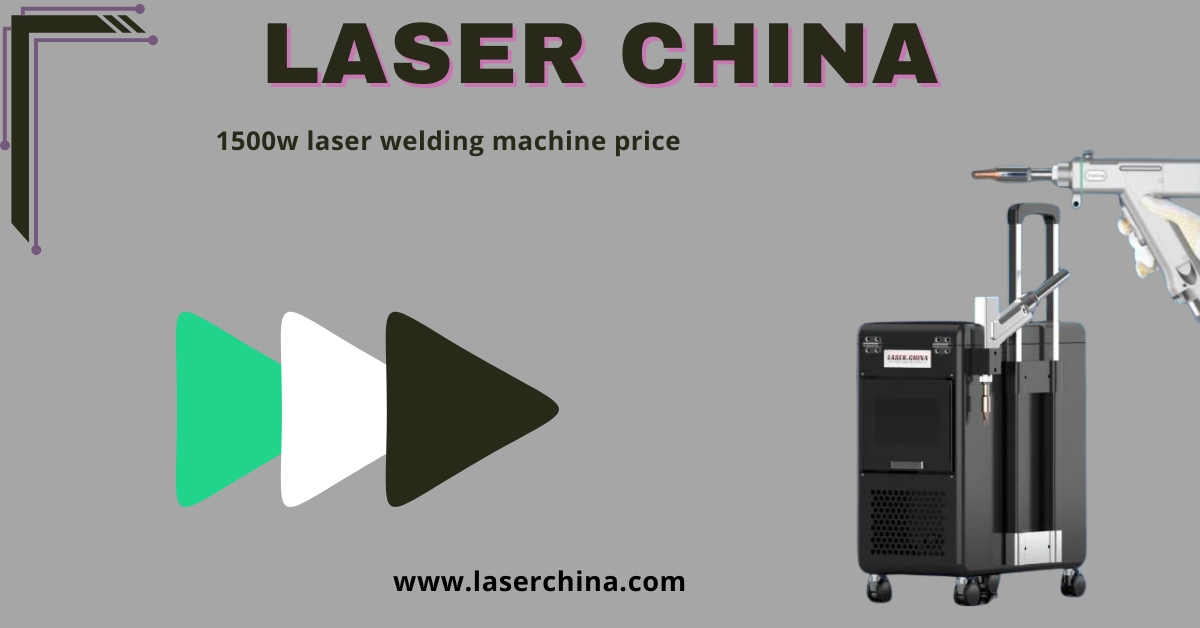
Laser welding equipment has revolutionized the welding industry with its advanced technology, precision, and efficiency. Compared to traditional welding tools, modern laser welding equipment offers a host of advantages that make it a superior choice for various applications. Below, we examine the key features and benefits of laser welding equipment and how it compares to conventional methods.
1. Key Features of Laser Welding Equipment
a. High-Precision Laser Technology
Laser welding equipment uses a highly focused laser beam to join materials. This technology allows for exceptional precision, making it ideal for applications requiring detailed and intricate welds, such as in the aerospace, medical, and electronics industries.
b. Versatility in Material Compatibility
Modern laser welding machines can handle a wide range of materials, including stainless steel, aluminum, copper, brass, carbon steel, titanium, and even dissimilar materials. This versatility makes them suitable for diverse industrial applications.
c. Adjustable Power and Settings
Most laser welding equipment offers adjustable power levels, beam focus, and pulse frequency, allowing users to customize the welding process to suit specific materials and project requirements. This adaptability enhances the efficiency and quality of welds.
d. Compact and Ergonomic Design
Contemporary laser welders, particularly handheld models, are designed to be portable and user-friendly. Their compact size and ergonomic handles make them easy to operate in tight or challenging spaces.
e. Minimal Maintenance Requirements
Laser welding machines are built for durability and require minimal maintenance compared to traditional welding tools. Their solid-state design ensures long-lasting performance and reduced downtime.
2. Benefits of Laser Welding Equipment
a. Superior Weld Quality
Laser welders produce clean, strong, and visually appealing welds with minimal splatter or defects. The precision of the laser beam minimizes the need for post-weld finishing, saving time and effort.
b. Reduced Heat-Affected Zone (HAZ)
Laser welding concentrates heat in a small, targeted area, significantly reducing the heat-affected zone. This feature minimizes distortion and preserves the integrity of the surrounding material, making it ideal for delicate or thin components.
c. High Speed and Efficiency
Laser welding is much faster than traditional methods like TIG and MIG welding. This speed boosts productivity and allows operators to complete projects in a fraction of the time.
d. Cost-Effectiveness
Although the upfront cost of laser welding equipment is higher than that of conventional welding tools, the long-term savings are substantial. Faster processing times, reduced material waste, and minimal rework needs contribute to a quick return on investment.
e. Eco-Friendly Operation
Laser welding equipment is environmentally friendly. It consumes less energy and generates minimal waste compared to traditional methods. Additionally, it often eliminates the need for consumables such as filler wires or shielding gases.
3. Comparison to Traditional Welding Tools
a. Accuracy
Traditional welding tools rely on manual skill, which can lead to inconsistencies. Laser welding equipment, on the other hand, delivers precise and uniform results, even for complex projects.
b. Application Range
While traditional tools are effective for certain tasks, they often struggle with intricate designs or hard-to-reach areas. Laser welders excel in such scenarios due to their focused beam and portability.
c. Operator Skill Requirement
Traditional welding methods require extensive training and experience. Laser welding equipment, with its intuitive controls and adjustable settings, is easier to learn and use effectively.
Conclusion
Modern laser welding equipment stands out for its precision, efficiency, and versatility. While it represents a higher initial investment, its long-term benefits, including superior weld quality, reduced costs, and environmental sustainability, make it a valuable asset across industries. Whether for small-scale workshops or large industrial operations, laser welding equipment is transforming the way materials are joined, setting a new standard for welding excellence.