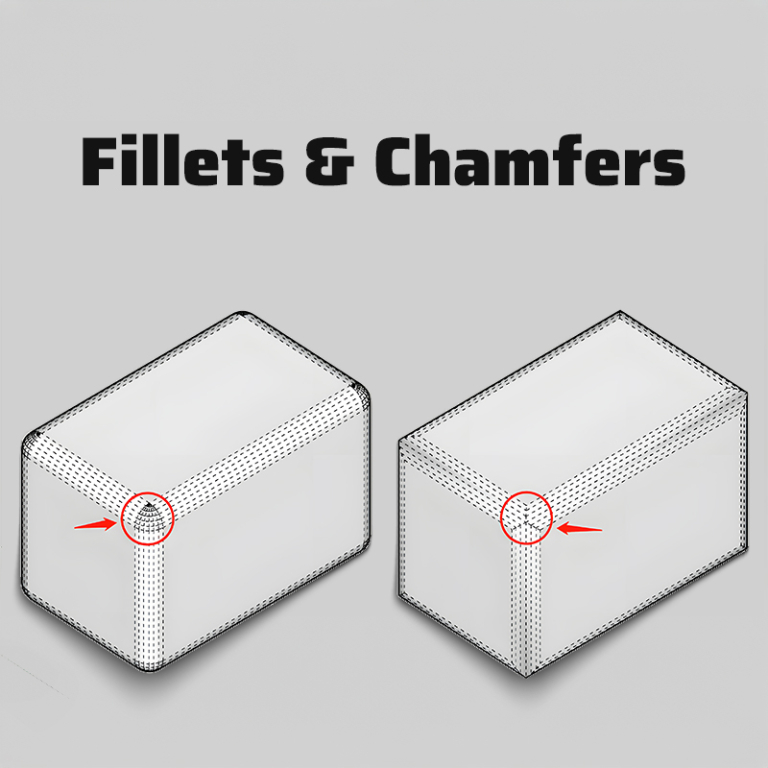
In the world of engineering, the design and manufacturing of parts require attention to detail, particularly when it comes to edge treatments. Chamfer and fillet are two common methods used to modify edges and corners in mechanical components. Though both techniques aim to improve functionality, safety, and aesthetics, they differ in their shape, purpose, and application. Knowing when to apply each is crucial to ensuring the success of a design.
This article will delve into the differences between chamfer vs fillet, explaining their characteristics, functions, common applications, and the factors to consider when choosing one over the other.
What is a Chamfer?
A chamfer refers to an edge that has been beveled or cut at a specific angle, typically 45 degrees, although other angles can be chosen depending on the requirements. Chamfers remove the sharp corner between two surfaces, creating a flat, slanted edge. This simple edge treatment serves both functional and aesthetic purposes and is relatively easy to manufacture.
Key Characteristics of Chamfers:
- Angle: Typically, chamfers are created at 45 degrees but can be made at other angles for different applications.
- Shape: Chamfers replace a sharp corner with a flat, slanted surface that is less likely to cause injury or damage.
- Manufacturing: Chamfers are easy to machine using common tools like mills, lathes, and drills, making them a cost-effective solution in many designs.
Common Applications of Chamfers:
- Assembly: Chamfers are often used in parts that need to fit together. For example, a chamfered hole makes it easier to insert a fastener or component into a part during assembly.
- Edge Protection: Chamfers remove sharp edges that could pose safety risks or cause wear and tear on other components.
- Stress Relief: While not as effective as fillets, chamfers can help in some cases to distribute stress more evenly across a part, preventing cracks or weaknesses at corners.
- Aesthetics: Chamfers can give a part a cleaner, more polished look, which is particularly important in consumer products or parts that are visible to users.
What is a Fillet?
A fillet is a rounded, curved transition between two surfaces, often used to replace sharp corners with a smooth curve. Unlike chamfers, fillets involve the addition of material to form a rounded corner, rather than cutting material away. Fillets are typically used to improve the structural integrity of a part by distributing stresses more evenly and preventing crack formation.
Key Characteristics of Fillets:
- Curve: Fillets create a smooth, rounded transition, either concave or convex, between two surfaces.
- Strength: The curved shape of a fillet distributes stress more evenly, which helps prevent the buildup of concentrated forces at corners and edges.
- Manufacturing: Fillets can be more challenging to produce than chamfers, as they require specific tools and machining techniques to create a smooth curve, especially when large radii are involved.
Common Applications of Fillets:
- Stress Relief: Fillets are commonly used in parts that undergo high stress or fatigue. The rounded edges eliminate sharp corners where stress could accumulate, thereby reducing the risk of cracks or fractures.
- Fluid Flow: In applications where fluids or gases pass over a part, fillets help to create smooth transitions, reducing turbulence and improving efficiency. They are commonly found in piping systems, aerodynamics, and HVAC systems.
- Strength Enhancement: Structural parts, such as beams or joints, often use fillets to improve their strength. The smooth transition helps distribute the forces more evenly, enhancing the component’s overall durability.
- Aesthetic Design: Fillets are often used in the design of consumer products where a smooth, rounded appearance is desired. This is common in industries like automotive, electronics, and furniture.
Chamfer vs Fillet: A Detailed Comparison
While chamfers and fillets are both used to modify the edges of a part, they serve different purposes and are best suited for different situations. The table below highlights the primary differences between the two:
Feature | Chamfer | Fillet |
---|---|---|
Shape | Beveled edge, flat surface at an angle | Rounded, curved edge |
Manufacturing Ease | Easier to machine, often with standard tools | More complex to manufacture, requires special tooling |
Stress Distribution | Less effective at stress relief | Excellent at stress distribution, prevents cracks |
Functionality | Used for edge protection, assembly, and aesthetics | Used for stress relief, fluid flow, and strength |
Common Applications | Assembly, threaded holes, and aesthetic purposes | Structural components, pipes, and high-stress parts |
Aesthetic Appeal | Can give a part a clean, angular appearance | Often used for smooth, sleek designs |
Choosing Between Chamfer and Fillet
The decision of whether to use a chamfer or a fillet depends on the specific requirements of your design. Below are key factors to consider when making your choice:
1. Part Function
- Chamfer: Chamfers are ideal when the part will be assembled with other components or when it is necessary to remove sharp edges for safety reasons. They are commonly used for functional parts that don’t face significant stress.
- Fillet: Fillets should be used in parts that are subjected to dynamic loads, fatigue, or high stresses. The rounded transition in a fillet helps reduce stress concentrations, making it a better choice for structural components.
2. Stress Distribution
- Chamfer: While chamfers can help with stress distribution to a degree, they are less effective than fillets in preventing cracks or fractures, especially in parts under heavy stress or loading.
- Fillet: Fillets are specifically designed to improve stress distribution. They are essential in high-stress areas, such as joints or beams, where crack formation could lead to failure.
3. Fluid Flow
- Chamfer: Chamfers are not typically used for fluid flow applications, as they do not create a smooth transition for liquids or gases.
- Fillet: Fillets excel in fluid dynamics applications, as the smooth curve reduces resistance and turbulence. This makes fillets ideal for pipes, aerospace components, and fluid transport systems.
4. Manufacturing Complexity
- Chamfer: Chamfers are generally easier and less expensive to manufacture, as they require only a simple angled cut. Standard machining processes can be used to create chamfers.
- Fillet: Fillets can be more challenging to produce, particularly when large radii are involved. Specialized tools, such as radii cutters or CNC machines, may be required to achieve the desired smooth curve.
5. Aesthetic Considerations
- Chamfer: Chamfers are often used for functional purposes, but they can also contribute to a clean, angular appearance in industrial designs.
- Fillet: Fillets are commonly used in consumer products and applications where a smooth, sleek look is desired. They add a more polished and elegant appearance to the design.
Conclusion
Both chamfers and fillets are vital edge treatments in mechanical design, each serving different purposes and offering unique benefits. Chamfers are more suitable for functional purposes such as assembly, safety, and stress relief in lower-stress components, while fillets are ideal for enhancing strength, durability, and fluid flow in high-stress or fatigue-prone parts. The choice between chamfer and fillet ultimately depends on the specific requirements of the part, including its function, stress exposure, and aesthetic needs.
By understanding the differences between chamfers and fillets, engineers and designers can make more informed decisions that lead to improved performance, efficiency, and safety in their products.