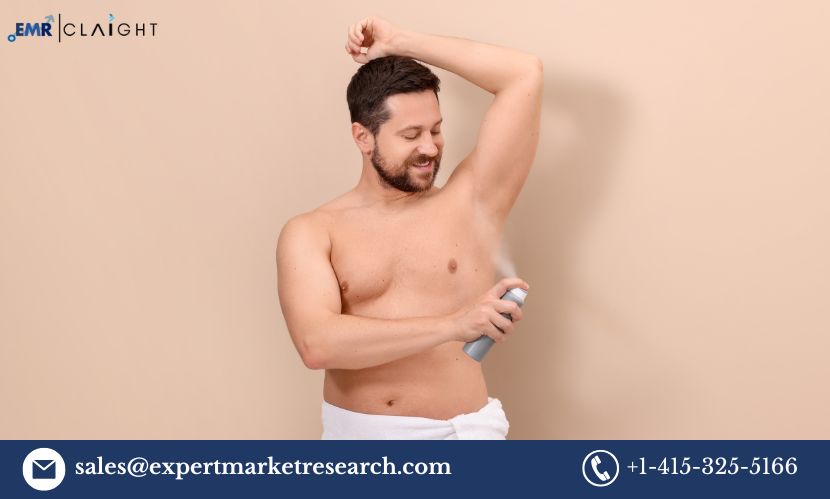
Introduction
A Deodorant Manufacturing Plant Project Report outlines the essential steps and considerations for setting up a facility dedicated to the production of deodorants. Deodorants, an integral part of personal care products, are widely used to prevent body odour caused by bacterial growth. With increasing consumer demand for personal hygiene products, deodorants represent a significant portion of the global cosmetics and toiletries market. This article covers the critical aspects of starting a deodorant manufacturing plant, including raw materials, production processes, market demand, and financial analysis.
What is Deodorant?
Deodorant is a personal care product used to mask or eliminate body odour, primarily caused by the bacteria that break down sweat. Deodorants come in various forms, such as sprays, roll-ons, sticks, gels, and creams. The primary ingredients typically include antimicrobial agents, fragrance, alcohol, and various emollients. The global deodorant market is growing rapidly due to an increasing awareness of personal hygiene, the rise in disposable income, and consumer preferences for fragrant, long-lasting products.
Why Set Up a Deodorant Manufacturing Plant?
The deodorant market is expanding worldwide due to an increasing awareness of personal hygiene and the growing focus on body care products. As more consumers adopt daily deodorant use, the demand for different types of deodorants, including natural, organic, and antiperspirant products, continues to rise.
A deodorant manufacturing plant allows companies to tap into this growing market by producing high-quality, diverse deodorant formulations that meet the needs of various consumer preferences. Additionally, advancements in packaging and the growing trend for eco-friendly, sustainable personal care products are opening new opportunities for businesses in this space.
Get a Free Sample Report with Table of Contents@
Market Demand and Growth
The global deodorant market has shown steady growth and is expected to continue expanding due to increasing consumer demand, innovations in formulations, and the rise in awareness regarding hygiene. As consumers become more conscious of the ingredients in personal care products, there is an increasing demand for natural, organic, and sustainable deodorants.
Key factors driving the deodorant market include:
- Growing Awareness of Hygiene: Consumers are becoming more aware of the importance of personal hygiene and body care.
- Rising Disposable Incomes: Increasing disposable income has allowed consumers to opt for higher-end and more diverse deodorant products.
- Innovation in Product Types: There is growing demand for innovative deodorant formats, such as roll-ons, sprays, and stick formulations.
- Natural and Organic Products: Consumers are increasingly opting for deodorants that use natural and organic ingredients, free from chemicals like aluminium and parabens.
Key Components of a Deodorant Manufacturing Plant
Setting up a deodorant manufacturing plant involves several critical steps, from sourcing raw materials to managing production processes. Below are the most important components of the project.
1. Raw Materials
The primary raw materials used in deodorant manufacturing include:
- Antimicrobial Agents: These prevent bacterial growth and help neutralise body odour. Common ingredients include triclosan or more natural alternatives like tea tree oil.
- Fragrances: Synthetic or natural fragrances are added to deodorants to mask body odour and provide a fresh scent.
- Alcohol: Acts as a solvent and carrier, particularly in spray deodorants. It also contributes to the antibacterial properties.
- Emollients: These provide a smooth texture and prevent irritation. Examples include glycerin, aloe vera, and various oils.
- Propellants: For spray deodorants, propellants such as butane or propane are used to expel the product from the can.
- Binders and Stabilisers: These help hold the deodorant together, especially in stick or gel formulations.
2. Production Process
The manufacturing process for deodorants generally follows these stages:
-
Formulation: The initial step involves creating the right mixture of active ingredients, fragrances, and solvents. This requires precise measurements and a careful blending process to ensure the deodorant’s effectiveness and consistency.
-
Mixing: In this step, the raw materials, including antimicrobial agents, fragrances, and alcohol (for sprays), are mixed together in large batches. The goal is to create a homogeneous mixture that can be easily processed.
-
Emulsification (for creams and gels): Emulsifying agents are used to create a stable product that combines oil and water-based ingredients.
-
Filling and Packaging: Once the deodorant has been formulated and mixed, it is transferred into its final packaging format, such as bottles, jars, spray cans, or sticks.
-
Quality Control and Testing: During production, rigorous testing is carried out to ensure that the deodorants meet industry standards for effectiveness, safety, and stability. This includes testing for skin irritation, fragrance longevity, and microbial activity.
3. Plant Design and Equipment
The plant design should support efficient production, with considerations for workflow, storage, and safety. Essential equipment includes:
- Mixing Tanks: For combining the raw materials into a consistent formulation.
- Emulsifiers and Homogenisers: Used in products that require emulsification, such as creams and gels.
- Filling Machines: To accurately dispense the product into containers, ensuring consistency in quantity and quality.
- Packaging Equipment: For sealing, labelling, and packaging the deodorant into its final product form.
- Quality Control Labs: To test the quality of the deodorant, including stability, fragrance strength, and safety.
4. Energy and Water Requirements
The deodorant manufacturing process can be energy-intensive, especially when using large mixing tanks and filling machines. Therefore, efficient use of energy and water is critical. The plant should implement energy-saving technologies and recycling systems to minimise waste and reduce operational costs.
5. Environmental Impact and Sustainability
Given the rising demand for eco-friendly products, manufacturers should consider sustainability in their deodorant production process. This can include sourcing natural and biodegradable ingredients, using recyclable or minimal packaging, and reducing carbon emissions from production processes. Adopting these green practices will not only meet consumer demand for sustainable products but also align with global environmental goals.
6. Quality Control and Testing
Ensuring high-quality products is crucial in the deodorant manufacturing process. Some of the most important quality control tests include:
- Skin Irritation Tests: To ensure that the deodorant does not cause allergic reactions or irritation when applied to the skin.
- Stability Testing: To check how the product performs over time, ensuring that it retains its fragrance and effectiveness.
- Microbial Testing: To verify that the product is free from harmful microorganisms, ensuring safety and hygiene.
7. Market Analysis and Forecasting
Before starting production, a market analysis is essential to understand consumer trends, competition, and demand in different geographic regions. Factors such as consumer preferences, pricing strategies, and marketing trends will help shape the production strategy. Additionally, forecasting future demand for deodorants, including growth in natural or organic variants, will help the plant scale efficiently.
8. Cost Analysis and Financial Projections
The financial feasibility of the deodorant manufacturing plant is a crucial consideration. Key aspects to analyse include:
- Capital Investment: For setting up the plant, purchasing machinery, and installing necessary infrastructure.
- Operational Costs: For raw materials, labour, energy consumption, maintenance, and packaging.
- Revenue Forecasts: Based on the expected market demand, production capacity, and pricing strategy.
- Break-even Point: Calculating how long it will take to recover the initial investment and start generating profits.
Safety and Compliance
Ensuring the safety of the workforce and compliance with industry standards is essential. The deodorant manufacturing plant must adhere to local and international safety regulations, including proper storage and handling of chemicals, equipment maintenance, and health and safety standards. Additionally, compliance with product regulations, such as the FDA or European Union Cosmetics Regulations, is mandatory.
Distribution and Marketing
Once the deodorants are manufactured, effective distribution and marketing strategies must be implemented. Establishing partnerships with retail stores, supermarkets, e-commerce platforms, and specialty retailers can ensure widespread product availability. Marketing efforts, such as digital campaigns, influencer partnerships, and sustainable product certifications, will attract consumers and enhance brand visibility.
FAQ
1. What are the main ingredients in deodorant?
The key ingredients in deodorants are antimicrobial agents, fragrances, alcohol, emollients, and sometimes propellants (for sprays).
2. What types of deodorants are most popular?
Spray deodorants, roll-ons, sticks, and gels are the most commonly used formats, each catering to different consumer preferences.
3. How is deodorant manufactured?
The manufacturing process involves mixing the ingredients, emulsifying (if necessary), and filling the product into its final packaging. Quality control is essential throughout.
4. What are the environmental concerns in deodorant manufacturing?
Environmental concerns include using non-recyclable packaging, harmful chemicals, and high water consumption. Eco-friendly production practices and packaging are increasingly in demand.
5. What are the challenges in setting up a deodorant plant?
Challenges include sourcing high-quality ingredients, adhering to regulations, managing energy consumption, and ensuring efficient production lines.
6. How can I forecast demand for deodorants?
Conducting market research, monitoring trends in personal care products, and evaluating regional preferences are crucial for accurate demand forecasting.
7. What are the safety concerns in deodorant production?
Safety concerns involve handling chemicals, ensuring proper equipment maintenance, and ensuring safe production processes to prevent accidents.
8. What is the market potential for deodorants?
The deodorant market is experiencing steady growth, driven by increasing awareness of hygiene and demand for eco-friendly products.
9. Is there a demand for natural deodorants?
Yes, consumers are increasingly seeking natural, organic deodorants that are free from chemicals like aluminium, parabens, and synthetic fragrances.
Media Contact:
Company Name: Claight Corporation
Contact Person: Lewis Fernandas, Corporate Sales Specialist — U.S.A.
Email: [email protected]
Toll Free Number: +1–415–325–5166 | +44–702–402–5790
Address: 30 North Gould Street, Sheridan, WY 82801, USA
Website: www.expertmarketresearch.com
Aus Site: https://www.expertmarketresearch.com.au