
In the fast-paced world of advanced manufacturing, precision, speed, and flexibility are paramount. As industries push the boundaries of what’s possible, manufacturers must equip their shops with the latest technologies to stay ahead of the competition. One such technology that has proven to be indispensable is the CNC rotary table.
A CNC rotary table is a powerful addition to any machining operation, enabling manufacturers to achieve greater versatility and precision in their production processes. This innovative tool is designed to rotate the workpiece, allowing for multi-axis machining that would be otherwise difficult or impossible to achieve with traditional setups. By integrating a CNC rotary table into your machining system, you can expand your capabilities, improve efficiency, and ensure that your parts meet the most stringent quality standards.
The Growing Importance of CNC Rotary Tables in Advanced Manufacturing
Manufacturers across various sectors, including aerospace, automotive, medical device manufacturing, and general machining, are always on the lookout for ways to optimize their production processes. Traditional methods of machining often require complex setups and multiple tool changes, leading to longer production times and higher costs. In contrast, CNC rotary tables streamline the machining process by allowing for continuous rotation and multiple-axis machining without the need for repositioning or manual adjustments.
This functionality is particularly valuable when machining intricate parts with complex geometries or multi-sided features. Without a CNC rotary table, manufacturers would need to perform multiple setups, often with different machines, to complete the various stages of machining. This process can be time-consuming, costly, and prone to errors. With a CNC rotary table, however, manufacturers can perform multi-axis operations in a single setup, reducing both time and labor costs while ensuring a higher level of precision.
How CNC Rotary Tables Work
A CNC rotary table is typically mounted on a machine’s bed and can rotate a workpiece along one or more axes. The rotation allows the machine tool to access various angles of the workpiece, enabling the machining of multiple sides without the need for repositioning. This capability is especially valuable for parts that require precision drilling, milling, or turning from multiple angles, such as complex aerospace components or multi-sided automotive parts.
CNC rotary tables are often combined with CNC machines such as vertical or horizontal milling machines, which offer the ability to perform simultaneous multi-axis machining. This combination of features helps streamline workflows and reduces the need for multiple machine setups. Many CNC rotary tables also include programmable controls, allowing operators to easily control the rotation speed, angle, and positioning of the workpiece, ensuring optimal accuracy and consistency.
Key Benefits of CNC Rotary Tables
Enhanced Precision and Accuracy
One of the primary benefits of CNC rotary tables is the ability to perform highly precise machining operations. The rotation mechanism ensures that the workpiece remains in a fixed position while the machine tool accesses various points on the part. This eliminates the need for re-clamping or repositioning, which can introduce errors or inconsistencies. As a result, CNC rotary tables help maintain a high level of accuracy throughout the machining process, producing parts that meet tight tolerances and quality standards.
Increased Machining Flexibility
CNC rotary tables allow manufacturers to perform a wide range of operations, such as milling, drilling, tapping, and grinding, from multiple angles. This flexibility is essential when working with complex geometries or parts that require multi-sided machining. With the ability to rotate the workpiece continuously, CNC rotary tables make it easier to perform operations on every surface, eliminating the need for multiple setups or tool changes. This increased versatility allows manufacturers to take on a broader range of projects and meet the demands of industries with high precision and tight deadlines.
Reduced Setup Times
Traditional machining often involves multiple steps and setups, which can lead to prolonged downtime between operations. With a CNC rotary table, manufacturers can reduce setup times significantly by performing multi-axis operations in a single setup. The workpiece can be rotated seamlessly throughout the machining process, eliminating the need to re-clamp or reposition it for each new operation. This reduction in setup time not only improves efficiency but also helps shorten lead times, allowing manufacturers to produce more parts in less time.
Improved Workflow and Productivity
By allowing for continuous rotation and multi-axis machining, CNC rotary tables streamline the entire manufacturing process. The ability to machine multiple sides of a part without repositioning reduces the overall time required for each project. This improvement in workflow leads to increased productivity, as fewer machine adjustments and tool changes are needed. Manufacturers can complete more jobs with less effort, which ultimately boosts throughput and helps reduce labor costs.
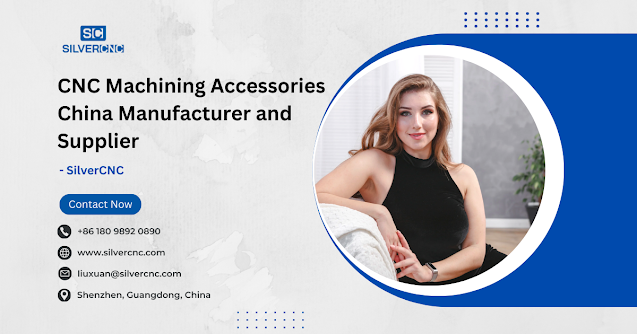
Higher Quality and Consistency
The ability to machine parts from multiple angles in a single setup results in higher-quality components. CNC rotary tables ensure that parts are machined to exact specifications, reducing the likelihood of errors caused by improper re-clamping or repositioning. As a result, manufacturers can maintain a higher level of consistency in their products, leading to fewer defects and less rework.
Cost Savings
Although CNC rotary tables represent an investment in new technology, they can lead to significant long-term cost savings. The reduction in setup times, tool changes, and labor costs makes it easier for manufacturers to increase their production capacity and profitability. Furthermore, the improved precision and quality reduce the need for costly rework or scrap, helping companies maintain better control over their operating costs.
Types of CNC Rotary Tables
Horizontal CNC Rotary Tables
Horizontal CNC rotary tables are typically mounted horizontally on the CNC machine and are ideal for applications where the workpiece requires precise rotation along the horizontal axis. These tables are commonly used in milling operations for parts with complex geometries that need to be accessed from different angles. Horizontal rotary tables are particularly valuable for machining heavy parts, such as large automotive components or industrial machinery.
Vertical CNC Rotary Tables
Vertical CNC rotary tables are mounted vertically and are often used for applications requiring vertical-axis rotation. These tables are ideal for smaller parts or applications that involve drilling, tapping, or engraving. Vertical CNC rotary tables are commonly used in the production of precision parts, such as medical devices, electronics, and small automotive components.
Indexing CNC Rotary Tables
Indexing CNC rotary tables are designed for applications where precise, incremental movement of the workpiece is required. These tables can be rotated to specific angles, allowing operators to perform operations on different sides of the part in a controlled manner. Indexing rotary tables are ideal for applications that require high precision but do not need continuous rotation throughout the entire machining process.
Dual-Axis CNC Rotary Tables
Dual-axis CNC rotary tables provide rotational movement along two axes, enabling manufacturers to perform complex multi-axis machining operations. These tables are often used in high-precision industries, such as aerospace or medical device manufacturing, where intricate parts with multi-sided features need to be machined with exceptional accuracy.
In the competitive world of advanced manufacturing, the ability to produce high-quality, precise parts in a timely manner is essential. CNC rotary tables offer manufacturers a powerful solution for achieving greater flexibility, accuracy, and efficiency in their machining operations. Whether you are working with complex geometries, multi-sided parts, or tight production schedules, a CNC rotary table can help streamline your workflow, reduce setup times, and improve overall productivity.
By integrating a CNC rotary table into your operation, you can enhance your machining capabilities and stay ahead in an increasingly demanding industry. As technology continues to evolve, the importance of CNC rotary tables in modern manufacturing will only continue to grow. Embracing this innovative technology will help ensure that your shop remains at the forefront of precision machining and continues to meet the needs of today’s advanced manufacturing world.
FAQs
- What is a CNC rotary table?
A CNC rotary table is a device used in CNC machining that allows for the continuous rotation of a workpiece along one or more axes, enabling multi-axis machining and improved precision.
- How does a CNC rotary table improve machining efficiency?
By allowing for continuous rotation and multi-axis machining, a CNC rotary table reduces the need for multiple setups, tool changes, and repositioning, resulting in faster production times and improved workflow.
- What industries benefit from CNC rotary tables?
CNC rotary tables are used across various industries, including aerospace, automotive, medical device manufacturing, and general machining, where precision, speed, and flexibility are critical.
- How does a CNC rotary table improve precision?
The rotation mechanism of a CNC rotary table ensures that the workpiece remains in a fixed position, reducing the likelihood of errors caused by re-clamping or repositioning, resulting in higher accuracy.
- Can a CNC rotary table be integrated with existing CNC machines?
Yes, CNC rotary tables can be integrated with a wide range of CNC machines, including vertical and horizontal milling machines, to enhance machining capabilities and improve production efficiency.