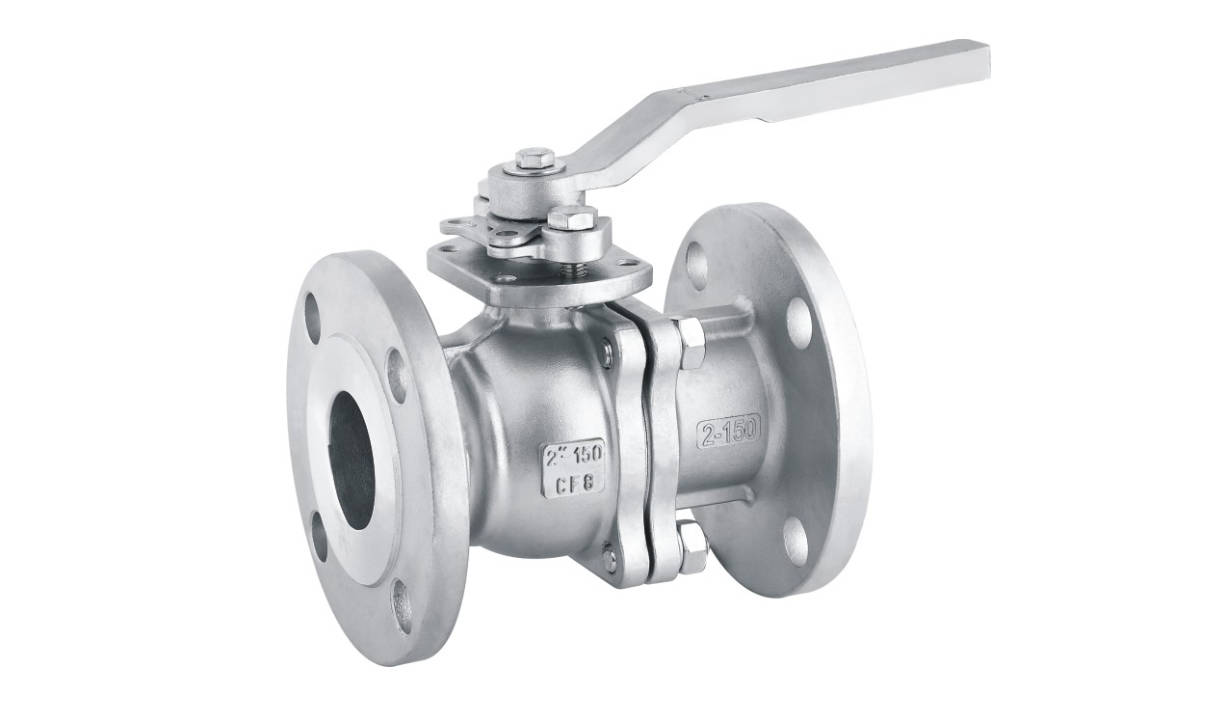
Comparative Analysis: Ball Valve vs Regular Valve
Operational Mechanisms
How Ball Valves Operate
Ball valves utilize a spherical disc, known as a ball, to control the flow of liquids or gases. The ball has a hole through the middle so that when the hole is aligned with both ends of the valve, flow will occur. When the valve is closed, the hole is perpendicular to the ends of the valve, blocking the flow. MIWIVAL ball valves are engineered to ensure bubble-tight shutoff and low operating torque. This design allows for quick operation and reliability in sealing.
Functionality of Regular Valves
Regular valves, which can include gate, globe, and butterfly valves among others, operate using different mechanisms. For instance, gate valves use a flat or wedge-shaped gate that slides in and out to control flow. Globe valves regulate flow through a movable plug that opens or closes against a stationary ring seat. These types typically offer more precise control over flow but can be slower to operate compared to ball valves.
Performance and Efficiency
Flow Control Efficiency in Ball Valves
Ball valves provide excellent flow control efficiency due to their simple quarter-turn operation which allows for quick opening and closing. The live load packing is self-adjusting due to its Belleville washers allowing it to compensate for environmental changes and wear, ensuring maintenance-free operation and long cycle life. This ensures that ball valves maintain their performance over time without frequent adjustments.
Performance Metrics for Regular Valves
Regular valves often excel in situations requiring precise flow regulation or throttling capabilities. However, they may not achieve the same level of tight shutoff as ball valves unless specifically designed for such applications. Their performance metrics will vary widely depending on the type of valve and its specific use case.
Durability and Maintenance Requirements
Longevity Factors for Ball Valves
Ball valves are known for their durability and minimal maintenance requirements. All resilient seat materials ensure bi-directional, bubble-tight sealing and feature relief slots on the seat outer diameter to relieve pressure past the upstream seat in case of an upset situation such as trapped gas in the valve body as well as positive preloading to ensure low pressure/vacuum sealing capability. This robust design contributes significantly to their longevity.
Maintenance Considerations for Regular Valves
Regular valves may require more frequent maintenance due to their more complex internal mechanisms. Components such as seals and seats might need regular inspection and replacement depending on usage conditions. This can lead to higher long-term maintenance costs compared to ball valves.
Selecting the Right Valve for Your Needs
Factors to Consider When Choosing a Valve
Application-Specific Requirements
When selecting between ball valves and regular valves, consider the specific application requirements such as pressure ratings, temperature conditions, and fluid characteristics. Ball valves are ideal for applications requiring fast action and reliable shutoff, while regular valves might be better suited for applications needing precise control over flow rates.
Environmental and Safety Considerations
Safety considerations are paramount when choosing a valve type. Ball valves are available as non-fire safe with standard stem seals or fire safe to API 607 with graphite stem seals, providing options depending on environmental safety needs.
Cost Implications and Budgeting
Initial Costs vs Long-Term Investment
While ball valves might have higher initial costs due to their robust design features like anti-static devices ensuring electrical continuity between the ball, stem, and body, they often represent a better long-term investment because of lower maintenance requirements.
Comparing Maintenance Costs
Regular valve types might initially be less expensive but can incur higher maintenance costs over time due to wear on moving parts that require replacement or repair more frequently than those in ball valves.
By understanding these key differences between ball valves and regular valves across operational mechanisms, performance efficiency, durability considerations, application-specific needs, environmental factors, cost implications, and maintenance requirements; professionals can make informed decisions tailored to their specific industrial applications.
Introduction to Miwival’s Advanced Valve Solutions
Miwival offers a range of valve products designed to meet the diverse needs of various industrial applications. Miwival flanged ball valve, known for their bubble-tight shutoff and low operating torque, provide reliable performance in numerous settings. These valves are engineered with features such as independent packing glands that can be easily adjusted without removing mounting hardware or the operator. This design ensures uniform load distribution across the packing, contributing to their long cycle life and maintenance-free operation.
Selecting the Right Valve for Your Needs
Factors to Consider When Choosing a Valve
Application-Specific Requirements
When choosing between ball valves and regular valves, it is crucial to consider the specific requirements of your application. Ball valves are particularly suited for applications requiring quick action and reliable shutoff. They feature resilient seat materials that ensure bi-directional, bubble-tight sealing and include relief slots on the seat’s outer diameter to relieve pressure past the upstream seat in case of an upset situation, such as trapped gas in the valve body. This design also provides positive preloading to ensure low-pressure/vacuum sealing capability.
Regular valves, on the other hand, maybe more appropriate for applications that demand precise flow regulation or throttling capabilities. The choice between these two types should be guided by factors such as pressure ratings, temperature conditions, and fluid characteristics specific to your application.
Environmental and Safety Considerations
Safety is a paramount consideration when selecting a valve type. Miwival ball valves are available in both non-fire-safe configurations with standard stem seals and fire-safe versions conforming to API 607 standards with graphite stem seals. This provides flexibility depending on the environmental safety needs of your application.
Cost Implications and Budgeting
Initial Costs vs Long-Term Investment
Ball valves might entail higher initial costs due to their robust design features such as anti-static devices ensuring electrical continuity between the ball, stem, and body, which eliminate the possibility of sparks within the valve created by static electrical charges. However, these features often translate into a better long-term investment because of reduced maintenance needs over time.
Conversely, regular valves may have lower upfront costs but could incur higher long-term expenses due to more frequent maintenance requirements. The complexity of their internal mechanisms means components like seals and seats might need regular inspection and replacement based on usage conditions.
Comparing Maintenance Costs
The maintenance costs associated with regular valves can be significant over time due to wear on moving parts that necessitate periodic repair or replacement. In contrast, ball valves are designed for durability with minimal maintenance requirements. For instance, Miwival’s ball valves incorporate live-loaded, self-adjusting stem seals that automatically adjust packing to compensate for changes in wear and temperature, further reducing maintenance demands.