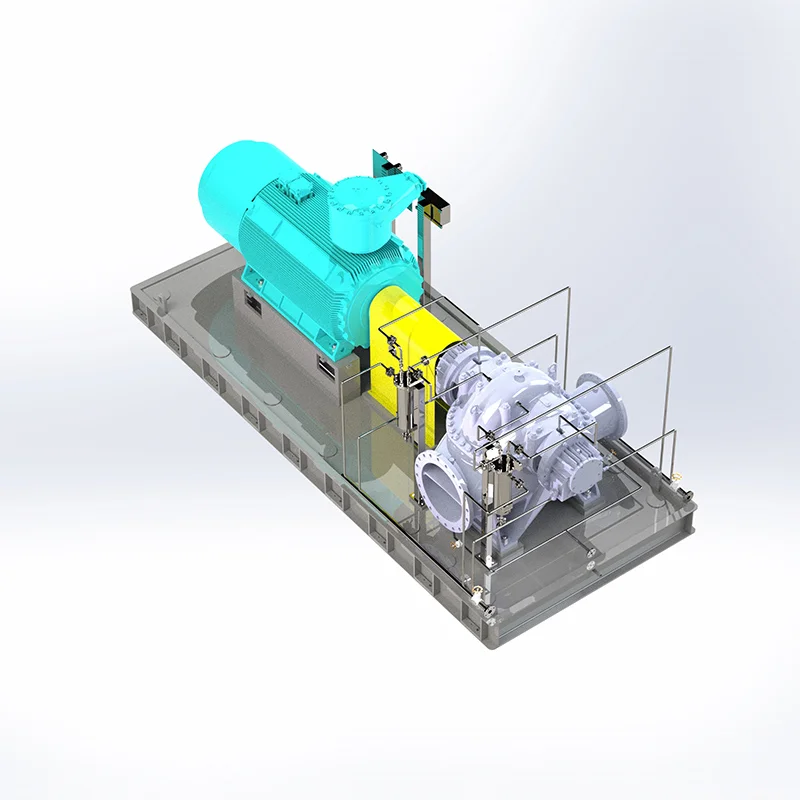
Comprehensive Handbook for Picking the Best Pump for Your Needs
Picking the pump for your needs can be quite a tough choice as the common query of “Which pump type is best suited?” often arises in such situations. However, the answer isn’t always straightforward as it varies depending on factors such as the properties of the fluid being handled and the required flow rate and pressure for the particular job at hand. This blog aims to explore the pump choices available along, with their unique features and where they excel in practical use cases.
What is a Pump?
To begin delving into the specifics of types of pumps, it’s essential to grasp the essence of what a pump is and its primary role beforehand. A pump serves as a device that moves liquids or gases using methods. There are mainly two categories of pumps to take into account: displacement pumps and centrifugal pumps.
Positive Displacement Pumps
Positive displacement pumps operate by trapping an amount of liquid and then pushing that sealed volume into the outgoing pipeline, known for their ability to handle fluids and uphold a consistent flow rate regardless of the pressure conditions.
Reciprocating pumps
Reciprocating pumps work by using a piston or diaphragm to move fluid forth in a cylinder, creating suction to draw fluid into the cylinder before pushing it out during each stroke rationally. This type of pump is best for applications requiring pressure and low flow rates, such as those found in hydraulic system upkeep or high-pressure cleaning tasks in the oil and gas industry.
Advantages: Skilled at managing high-stress scenarios with regulation of liquid flow and proficiency in handling viscous substances effectively.
Drawbacks: Occasionally the flow might fluctuate and may require using tools to maintain functioning. Moreover, there could be a need for more frequent maintenance due to moving parts being present.
Rotary pumps
Rotary pumps work by using moving parts such as gears or screws to create motion and generate suction that draws in fluid into the pump housing before circulating it and pushing it out through the outlet port. These pumps are commonly used with liquids such as oils and syrups in industries like chemical processing and food production due to their efficiency and ease of upkeep.
Advantages: These devices help maintain the flow of thick liquids and need little maintenance.
Drawbacks: Individuals might find it challenging to cope with demanding assignments. May experience quicker wear and tear when dealing with harsh liquids.
Centrifugal Pumps
In industries, centrifugal pumps are frequently utilized as the main pump type, which operates by transforming kinetic energy into hydrodynamic energy to propel the fluid forward.
Advantages: It includes a layout that requires minimal upkeep and operates efficiently with thin fluids.
Drawbacks: They struggle with fluids and are not ideal for high-pressure tasks.
Multi-stage centrifugal pumps
Multi-stage centrifugal pumps operate by arranging impellers in a sequence to increase fluid pressure as it passes through each impeller stage to achieve greater pressure outputs efficiently. These pumps are well suited for tasks requiring pressure levels such as boiler feed water systems and high-pressure washing applications.
Advantages: They offer the advantage of managing pressure levels and are suitable for high-flow tasks while also being compact in design.
Drawbacks: A complex design can result in higher upfront costs and increased maintenance requirements.
Diaphragmatic pumps
Diaphragm pumps work by using a membrane that moves back and forth to create a temporary space for taking in and pushing out liquids using various mechanical methods or hydraulic and compressed air systems. They are well suited for handling fluids and thick substances and are commonly used in industries like chemical processing plants and wastewater treatment facilities, as well as in the food and beverage sector.
Advantages: It is adept at handling fluids without requiring seals, such as solids to avoid leaks.
Cons: The limitations include constraints on flow rates and pressure capabilities as well, as potential wearing out of diaphragms over extended periods of use.
Peristaltic pumps
Peristaltic pumps work by using a rotating roller or shoe to compress a tube, creating a vacuum that draws fluid through before pushing it out as the roller moves along the length of the tube. These pumps are great for applications requiring dosages, such as in medical and laboratory settings, and for handling sensitive fluids that can be affected by shear forces. One of their advantages is that there is no risk of contamination, as the liquid only touches the tube, making it easy to maintain with tubes.
Advantages: The pump operates smoothly as it is submerged. Does not need priming.
Downsides: The flow rates and pressure capacities are limited. There is a chance of the tubes deteriorating over time.
Factors to Consider When Choosing a Pump
Once you’ve thoroughly researched pump choices, it’s important to consider the factors that will influence your decision on selecting the right pump for your needs.
Characteristics of Fluids
Thickness: The thickness of the liquid influences the choice of pump to be used well. When dealing with fluids such as oils and syrups it is advisable to utilize positive displacement pumps; in contrast thinner liquids, like water, are better handled by centrifugal pumps.
Corrosive Nature
If you’re working with liquids in your system arrangement and need a pump that can withstand the effects of corrosion over time, it’s best to choose a pump made from materials such as steel or those coated with specialized protection layers.
Flow Rate and Pressure Needs
When selecting the size and kind of pump to use for your needs and application requirements, consider the volume of fluid that needs to be transferred within a given time frame. Additionally, it is important to factor in the pressure to propel the liquid through your system as this will influence the choice of pump best suited for your needs.
Energy Efficiency
When looking at how pumps consume power when they run nonstop, it’s important to think about the kind of pump in use. Centrifugal pumps are usually more energy efficient for jobs that need a flow and low pressure, while positive displacement pumps are better for tasks with high pressure and low flow.
Maintenance Convenience
Some pumps, like pumps, are easier to take care of due to their simple design and readily replaceable parts when compared to others, such as multi-stage centrifugal pumps, which may require more frequent and complex maintenance procedures.
Which Type of Pump is Best?
Choosing the right pump type is not a decision as it depends on various factors like the properties of the liquid being pumped and considerations such as flow rate and pressure requirements tailored to your unique application needs and energy efficiency goals while also taking maintenance into account.
When working with liquids and requiring control of flow rates it is generally advised to opt for positive displacement pumps such as reciprocating or rotary pumps. In cases where there is a demand for flow but at pressures, centrifugal pumps, particularly single-stage models, are commonly seen as the most efficient and cost-effective selection. For particular requirements, diaphragm pumps or peristaltic pumps may be better-suited choices depending on the specific needs of your application.
Understanding the types of pumps and their applications in different situations allows you to confidently select the appropriate one that ensures consistent and reliable operation, customized to suit your specific requirements.
Advantages: They offer the advantage of managing pressure levels and are suitable for high-flow tasks while also being compact in design.
Drawbacks: A complex design can result in higher upfront costs and increased maintenance requirements.
Diaphragmatic pumps
Diaphragm pumps work by using a membrane that moves back and forth to create a temporary space for taking in and pushing out liquids using various mechanical methods or hydraulic and compressed air systems. They are well suited for handling fluids and thick substances and are commonly used in industries like chemical processing plants and wastewater treatment facilities, as well as in the food and beverage sector.
Advantages: It is adept at handling fluids without requiring seals, such as solids to avoid leaks.
Cons: The limitations include constraints on flow rates and pressure capabilities as well, as potential wearing out of diaphragms over extended periods of use.
Peristaltic pumps
Peristaltic pumps work by using a rotating roller or shoe to compress a tube, creating a vacuum that draws fluid through before pushing it out as the roller moves along the length of the tube. These pumps are great for applications requiring dosages, such as in medical and laboratory settings, and for handling sensitive fluids that can be affected by shear forces. One of their advantages is that there is no risk of contamination, as the liquid only touches the tube, making it easy to maintain with tubes.
Advantages: The pump operates smoothly as it is submerged. Does not need priming.
Downsides: The flow rates and pressure capacities are limited. There is a chance of the tubes deteriorating over time.
Factors to Consider When Choosing a Pump
Once you’ve thoroughly researched pump choices, it’s important to consider the factors that will influence your decision on selecting the right pump for your needs.
Characteristics of Fluids
Thickness: The thickness of the liquid influences the choice of pump to be used well. When dealing with fluids such as oils and syrups it is advisable to utilize positive displacement pumps; in contrast thinner liquids, like water, are better handled by centrifugal pumps.
Corrosive Nature
If you’re working with liquids in your system arrangement and need a pump that can withstand the effects of corrosion over time, it’s best to choose a pump made from materials such as steel or those coated with specialized protection layers.
Flow Rate and Pressure Needs
When selecting the size and kind of pump to use for your needs and application requirements, consider the volume of fluid that needs to be transferred within a given time frame. Additionally, it is important to factor in the pressure to propel the liquid through your system as this will influence the choice of pump best suited for your needs.
Energy Efficiency
When looking at how pumps consume power when they run nonstop, it’s important to think about the kind of pump in use. Centrifugal pumps are usually more energy efficient for jobs that need a flow and low pressure, while positive displacement pumps are better for tasks with high pressure and low flow.
Maintenance Convenience
Some pumps, like pumps, are easier to take care of due to their simple design and readily replaceable parts when compared to others, such as multi-stage centrifugal pumps, which may require more frequent and complex maintenance procedures.
Which Type of Pump is Best?
Choosing the right pump type is not a decision as it depends on various factors like the properties of the liquid being pumped and considerations such as flow rate and pressure requirements tailored to your unique application needs and energy efficiency goals while also taking maintenance into account.
When working with liquids and requiring control of flow rates it is generally advised to opt for positive displacement pumps such as reciprocating or rotary pumps. In cases where there is a demand for flow but at pressures, centrifugal pumps, particularly single-stage models, are commonly seen as the most efficient and cost-effective selection. For particular requirements, diaphragm pumps or peristaltic pumps may be better-suited choices depending on the specific needs of your application.
Understanding the types of pumps and their applications in different situations allows you to confidently select the appropriate one that ensures consistent and reliable operation, customized to suit your specific requirements.