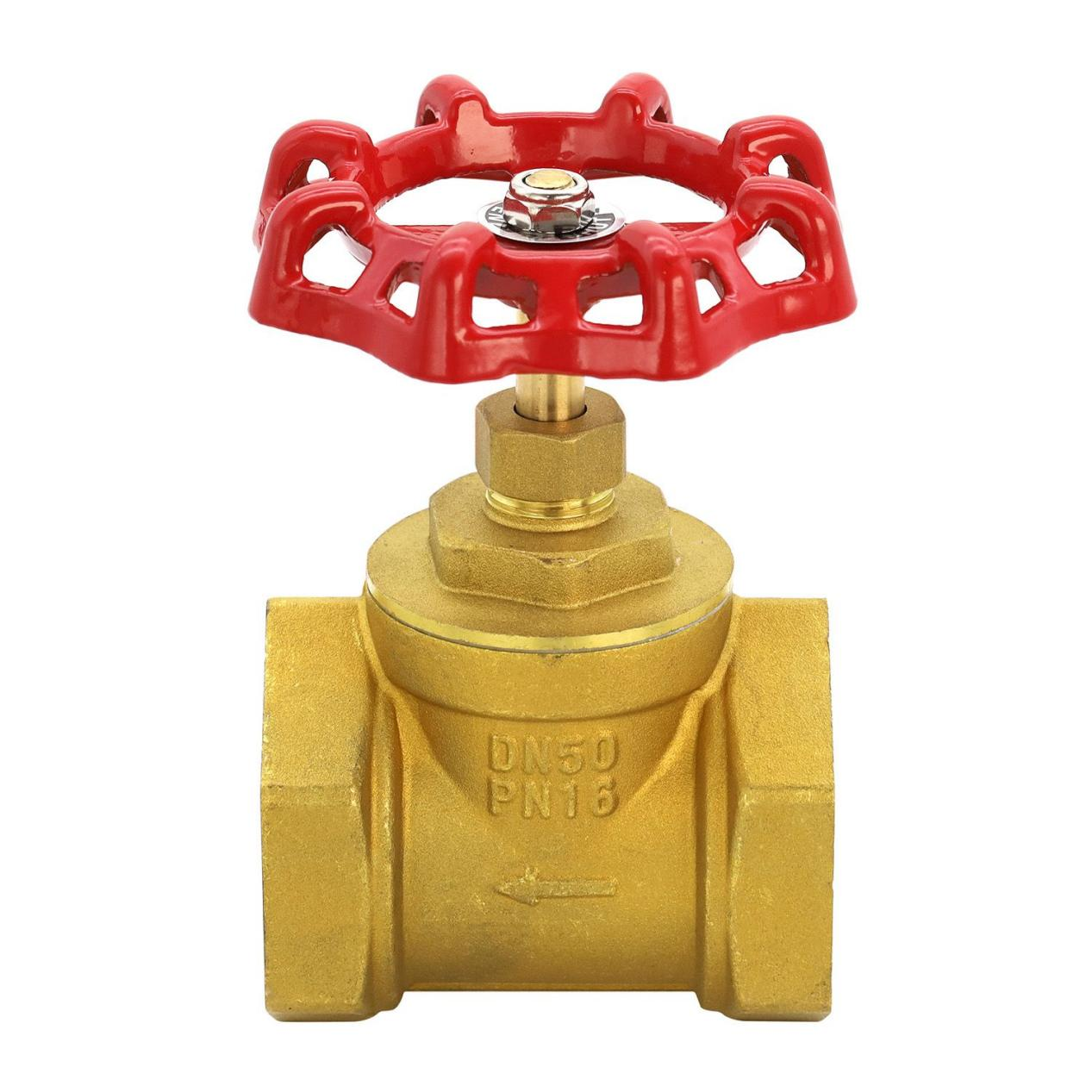
Composition and Characteristics of Brass Valves
Material Composition of Brass Valves
Alloy Components
Brass valves are mainly made of a combination of copper and zinc which are the key components of brass alloy used in different applications based on the varying ratio of these elements included in their composition. Additional elements like lead may also be added to improve machinability and performance, in certain industrial settings.
Advantages of Brass Material
Brass material offers several advantages that make it suitable for valve manufacturing. Its excellent machinability allows for precise fabrication, while its ductility ensures ease of forming into complex shapes. Moreover, brass exhibits good thermal conductivity, making it ideal for applications requiring efficient heat transfer. The material’s aesthetic appeal is an added benefit in visible installations.
Mechanical Properties of Brass Valves
Strength and Durability
Brass valves are known for their durable nature attributed to the unique qualities of brass alloy they possess. This strength enables the valves to endure high-pressure conditions without bending or breaking. Additionally, the durability of the material means that the valves have a lifespan reducing the frequency of replacements needed.
Corrosion Resistance
Brass valves are known for their ability to resist corrosion effectively due to the zinc content in the alloy that creates a coating on the valve surface to shield it from oxidation and degradation caused by moisture and chemical exposure This resistance plays a vital role, in ensuring the long term functionality of the valves under challenging environmental conditions.
Types of Brass Valves and Their Functions
Ball Valves
Design and Mechanism
Ball valves have a design feature, with a spherical closure unit that regulates the flow through a central cavity. These valves can open or close fluid pathways by rotating the ball by 90 degrees. This mechanism ensures shut-off capabilities while maintaining minimal pressure drop.
Common Uses in Industry
Ball valves are commonly found in a variety of industries because of their flexibility, in use They are frequently utilized in situations that demand sealing and fast functionality like water distribution systems chemical plants, and oil refineries.
Gate Valves
Operational Features
Gate valves function by raising a gate to clear the fluids pathway, which minimizes flow hindrance when fully open but necessitates operating space in contrast to other valve varieties. I am ideally suited for controlling flow states rather than regulating fluid movement gate valves exhibit exceptional effectiveness, in binary control operations.
Application Scenarios
These valves are usually employed in situations where they are not frequently used. For example, in isolating sections of pipelines or systems that need an uninterrupted flow of fluids.
Check Valves
Functionality and Benefits
Check valves allow liquid to flow in one direction while stopping it from flowing the other way to protect machinery from harm due to reverse flow pressure, with a basic setup comprising a disc or ball that closes automatically when there is back pressure present.
Typical Use Cases
Check valves are commonly utilized in a variety of settings such, as water supply systems and industrial processes to prevent backflow and uphold the integrity of the system.
Manufacturing Process of Brass Valves
Casting Techniques for Brass Valves
Sand Casting Process
Sand casting is a process where a mold is made using sand and then molten brass is poured into it to create valve components. This method is affordable, for making shapes but it might need some extra machining to get the exact dimensions right.
Die Casting Process
In indie-casting processes, metal molds are utilized to inject brass at high pressure resulting in the creation of parts with excellent surface quality and precise dimensions when compared to sand casting techniques ideal, for producing a high quantity of pieces efficiently.
Quality Control Measures in Production
Inspection Procedures
In the production of brass valves quality control is implemented through inspection processes such as checking dimensions pressure testing and visual examinations to guarantee that each valve meets the required standards prior, to being delivered to customers.
Standards Compliance
Manufacturers need to follow industry guidelines like ASTM or ISO requirements when creating products to ensure their reliability and safety, for uses.
Applications of Brass Valves Across Industries
Plumbing and Water Supply Systems
Residential Plumbing Uses
Brass valves are commonly used in household plumbing systems for their durability and ability to resist corrosion effectively when regulating water flow, in homes.
Industrial Water Management
Brass valves are essential in environments for effectively controlling extensive water supply systems because they can withstand high pressures and last long despite constant wear and tear, from usage.
HVAC Systems
Role in Heating Systems
Brass valves in heating systems effectively adjust the flow of water to maintain optimal temperatures, in buildings and withstand corrosion caused by heated liquids.
Air Conditioning Applications
Brass valves are used in air conditioning systems to control the flow of refrigerant helping to create energy-efficient climate control solutions, for commercial buildings.
Gas and Oil Industries
Pipeline Installations
In the gas and oil industries brass valves play a role in ensuring the safe transportation of materials by offering dependable shut-off systems, in pipeline setups. This helps reduce the risks of leaks or ruptures that could occur under high-pressure conditions commonly found in these operational environments.
Safety Considerations
When working with gas and oil extraction and refining processes it is important to choose valve designs that can manage the pressures and temperatures involved to ensure safety and comply with industry regulations worldwide.
Maintenance and Longevity of Brass Valves
Routine Maintenance Practices
Cleaning Procedures
In cleaning routines, it is important to clear away any accumulated debris, near the moving parts to keep them running smoothly prolonging the lifespan of the components and maintaining the system’s overall efficiency.
Lubrication Needs
Address the lubrication needs regularly by applying lubricants to reduce friction between moving parts, which helps prevent wear and tear while improving performance and reliability, over time.
Troubleshooting Common Issues
Leak Detection Methods
Methods, for detecting leaks involve inspecting, conducting pressure tests, ts and spotting potential leaks in the early stages to avoid costly repairs later on.
Repair Techniques
To fix things you need to swap out parts and seal any leaks, with the right materials to make sure everything works properly and stays safe and efficient.