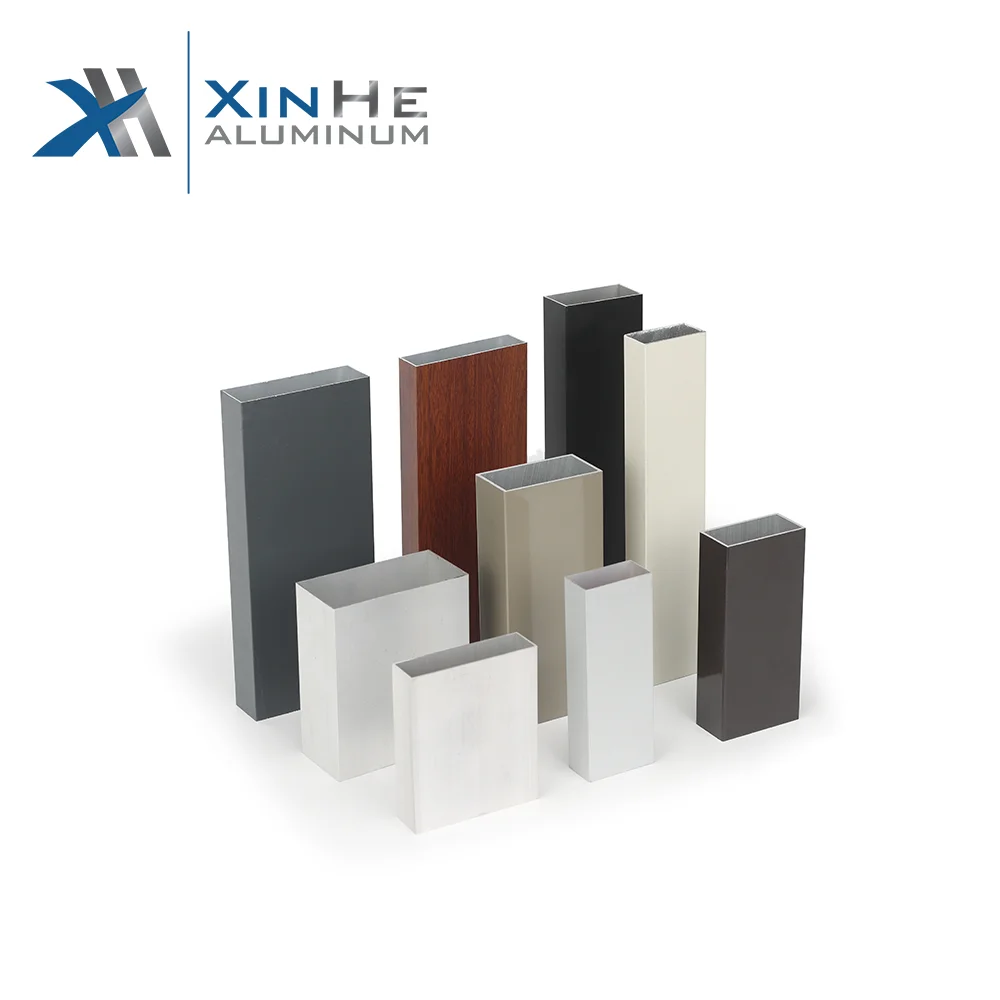
CNC machining has revolutionized the manufacturing world by enabling the simple production of parts. In order to get the most out of the technology, one ought to understand how to design parts for CNC machining. The blog gives perspective on best practices and considerations that will not only render your designs manufacturable but also cost-effective and engineered for the best performance.
Grasping CNC Machining Capabilities and Limitations
While starting to create a product or project on CNC machining technology, one must get an idea of the general characteristics and limitations of this manufacturing process. Using materials is key in machining work with CNC machines. They can handle everything from metals like steel and aluminum to plastics and wood with ease because of their versatility and adaptability. Such flexibility is also dependent to a great degree on the specific characteristics of the material being used in dictating the machining methods and tools to employ.
Crafting shapes showcases the true strength of CNC machining technology effortlessly handling intricate 3D curves and intricate details such as pockets and holes without breaking a sweat! However, challenges arise when dealing with angles or navigating tight corners within the design’s inner structure. This is where additional tools or finishing touches might be necessary for a flawless finish.
Precision is a hallmark of CNC machining allowing for the attainment of tolerances and refined surface finishes through careful selection of machine accuracy and tools that align with the properties of the materials being worked on.
Basic Design Considerations for CNC Machining
CNC machining has revolutionized modern manufacturing with unprecedented accuracy, versatility, and productivity in the manufacture of complex parts. To gain full advantage from this advanced technology, however, awareness of the key design considerations is essential. From material selection and geometric constraints to tolerances and surface finishes, all aspects of your design have a bearing on manufacturability, cost, and performance of the finished part.
1. Material Selection:
In choosing materials to be machined take note of their machinability rating indicating how easy they are to machine and how much they reduce tool wear like the ease of machining aluminum alloys versus stainless steel options.
Aspects to be considered are how much strength and hardness the part requires in order to function well and what the cost and availability of the materials are so that the project costs less.
2. Geometric Design:
Avoid navigating inside corners as they can pose challenges, for machinery and potentially lead to tool malfunctions. Instead, opt for curves that align with the dimensions of the cutting tool you intend to utilize.
Minimize the effects of walls and pockets with significant depth during machining by dealing with vibration challenges in thin walls and the necessity, for specialized tools and more time when working on deep pockets.
Ensure efficiency in hole design by selecting sizes and depths that match standard drill bits reducing the need, for frequent tool changes and saving time during machining processes.
Be sure to consider the angles of drafts when creating components that will be taken out of molds as they play a role, in facilitating the extraction process.
3. Feature Accessibility:
When creating features it’s important to think about tool accessibility to prevent shapes that could limit the range of motion of cutting tools.
Strive to create designs that can be easily produced using setups to reduce manufacturing time and costs.
4. Tolerances and Surface Finish:
Consider tolerances and avoid stringent tolerances as they may result in extended machining durations and increased costs. Have a conversation with your CNC machining service provider to determine tolerances tailored to your requirements.
In the design planning on your project surface finishes, you should decide on the finish you require at the onset, because it will have an effect on the tools to be used and machining processes to be followed.
Design for Manufacturability (DFM) Principles
l Conforming to DFM guidelines ensures that your designs are CNC machined efficiently and at the lowest possible cost:
l Keep your designs simple by limiting the number of features and complex shapes you incorporate.
l Enhance our production process by utilizing sizes and features to reduce the reliance, on customized tools and decrease the time spent on machining tasks.
l Boost productivity cut down waste and tactically organize components to optimize materials usage and minimize leftover waste.
Leveraging CAD Software for CNC Machining Design
CAD software plays a role, in designing CNC machining processes.
l Craft detailed 4 designs of your components by including all essential attributes and measurements.
l Utilizing simulation tools to examine aspects such as stress distribution, vibrations, and heat generation, for analysis.
l Connect seamlessly with Computer Aided Manufacturing (CAM) programs to generate toolpaths and instructions, for machining tasks.
Collaborating with Your CNC Machining Partner
Ensuring communication, with your CNC machining supplier is essential. At the beginning of the design process make sure to communicate with your machining partner to tap into their expertise and address any obstacles proactively. Gazing through designs is essential to determine and correct any flaws related to the manufacturing processes. It is advisable to prototype first before going into mass production, to test and refine your design so that you can identify where the areas of improvement are.
Conclusion
Parts machining design on a CNC machine must possess a thorough understanding of the technology’s strengths and limitations, and of the correct material choice, geometric shape, feature access, tolerance, and surface finish. By sticking to DFM principles, employing CAD software, and coordinating very closely with your CNC machining vendor, you can design parts not only producible but also cost-effective, high-performance, and high-quality optimized. Embrace these principles to exploit the potential of CNC machining and achieve your inventive designs.
Do remember that this is just an overview of the subject matter. For design advice and professional consultation on using CNC machining techniques, it is recommended to approach experienced personnel, with years of experience and the finest machinery to walk you through the nuances of CNC machining, for improved results.