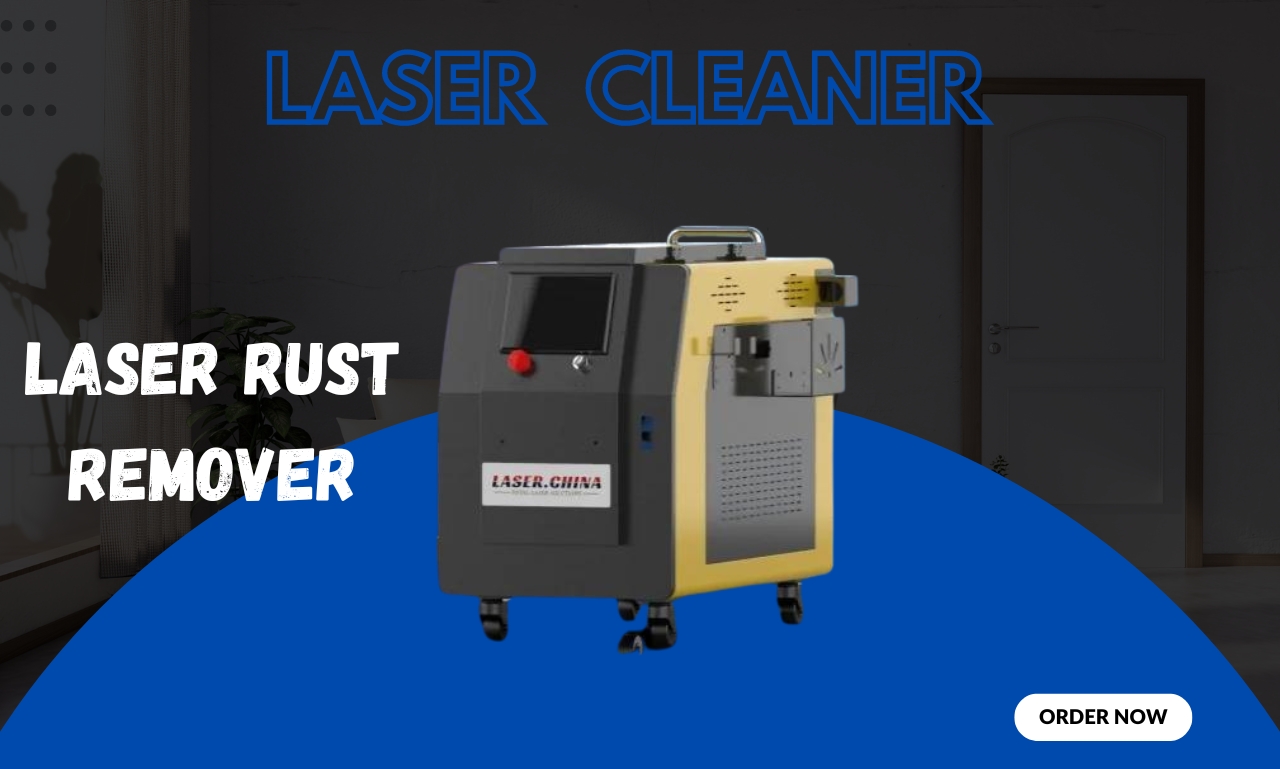
A metal laser cutting machine is an advanced industrial tool that uses a high-powered laser beam to cut, engrave, or shape various metals with extreme precision. It is widely used in industries such as automotive, aerospace, construction, and custom metal fabrication due to its efficiency, accuracy, and ability to handle complex designs. Compared to traditional cutting methods like plasma or waterjet cutting, laser cutting provides higher precision, minimal material waste, and faster processing speeds.
1. How Does a Metal Laser Cutting Machine Work?
A metal laser cutting machine operates using a concentrated laser beam that melts, burns, or vaporizes the metal to create precise cuts. The process involves several key steps:
-
Laser Beam Generation: A laser source (fiber, CO₂, or Nd:YAG) generates a high-intensity laser beam.
-
Beam Focusing: The laser is focused into a fine point using lenses or fiber optics, increasing its energy density.
-
Material Interaction: The laser heats and melts the metal along the cutting path.
-
Assist Gas Ejection: Compressed gases like oxygen, nitrogen, or air blow away molten metal, preventing oxidation and ensuring clean cuts.
-
CNC Control: Computer-controlled motion systems guide the laser beam for precise cutting based on programmed designs.
2. Types of Metal Laser Cutting Machines
There are three main types of laser cutting machines used for metal processing:
-
Fiber Laser Cutting Machines:
-
Highly efficient and energy-saving.
-
Best for cutting stainless steel, aluminum, copper, and brass.
-
Provides faster cutting speeds and lower operating costs compared to CO₂ lasers.
-
-
CO₂ Laser Cutting Machines:
-
Uses a gas mixture (CO₂) to generate the laser beam.
-
Works well for cutting both metals and non-metal materials like wood and acrylic.
-
Requires more maintenance due to mirrors and gas usage.
-
-
Nd:YAG Laser Cutting Machines:
-
Utilizes a solid-state laser.
-
Ideal for high-precision applications like medical devices and aerospace components.
-
Less common than fiber and CO₂ lasers.
-
3. Advantages of Using a Metal Laser Cutting Machine
Metal laser cutting machines offer numerous benefits that improve manufacturing efficiency and product quality:
-
High Precision: Achieves accuracy up to ±0.01mm, allowing for intricate cuts and fine details.
-
Faster Cutting Speeds: Compared to mechanical cutting, laser technology operates at much higher speeds, increasing productivity.
-
Minimal Material Waste: The narrow laser beam reduces kerf width, maximizing material utilization.
-
Smooth and Clean Edges: No need for additional finishing, reducing processing time and costs.
-
Versatile Material Compatibility: Cuts various metals, including steel, aluminum, titanium, and copper.
-
Automation and Integration: Can be integrated with CNC systems for seamless manufacturing processes.
4. Factors Affecting Metal Laser Cutting Performance
To achieve the best cutting results, several factors must be considered:
-
Laser Power: Higher wattage enables cutting thicker metals.
-
Cutting Speed: Proper speed settings prevent overheating and ensure clean cuts.
-
Assist Gas Selection:
-
Oxygen: Speeds up cutting for carbon steel but may cause oxidation.
-
Nitrogen: Produces clean, oxidation-free cuts, ideal for stainless steel and aluminum.
-
Air: Cost-effective but less effective for thick metals.
-
-
Focus and Beam Alignment: Precise focus ensures consistent and high-quality cutting results.
5. Maintenance and Safety Considerations
To keep a metal laser cutting machine in optimal condition, regular maintenance and safety measures should be followed:
-
Regular Cleaning: Keep lenses, mirrors, and nozzles clean to avoid beam distortion.
-
Cooling System Monitoring: Proper cooling prevents laser source overheating.
-
Protective Gear: Operators should wear safety glasses and follow laser safety guidelines.
-
Proper Ventilation: Removes metal fumes and debris generated during the cutting process.
6. Conclusion
A metal laser cutting machine is an essential tool in modern manufacturing, offering unparalleled precision, speed, and efficiency. Its ability to cut a wide range of metals with minimal waste makes it a valuable asset for industries requiring high-quality and cost-effective metal processing. By choosing the right type of laser, optimizing cutting parameters, and following proper maintenance practices, businesses can significantly enhance productivity and achieve superior cutting results.