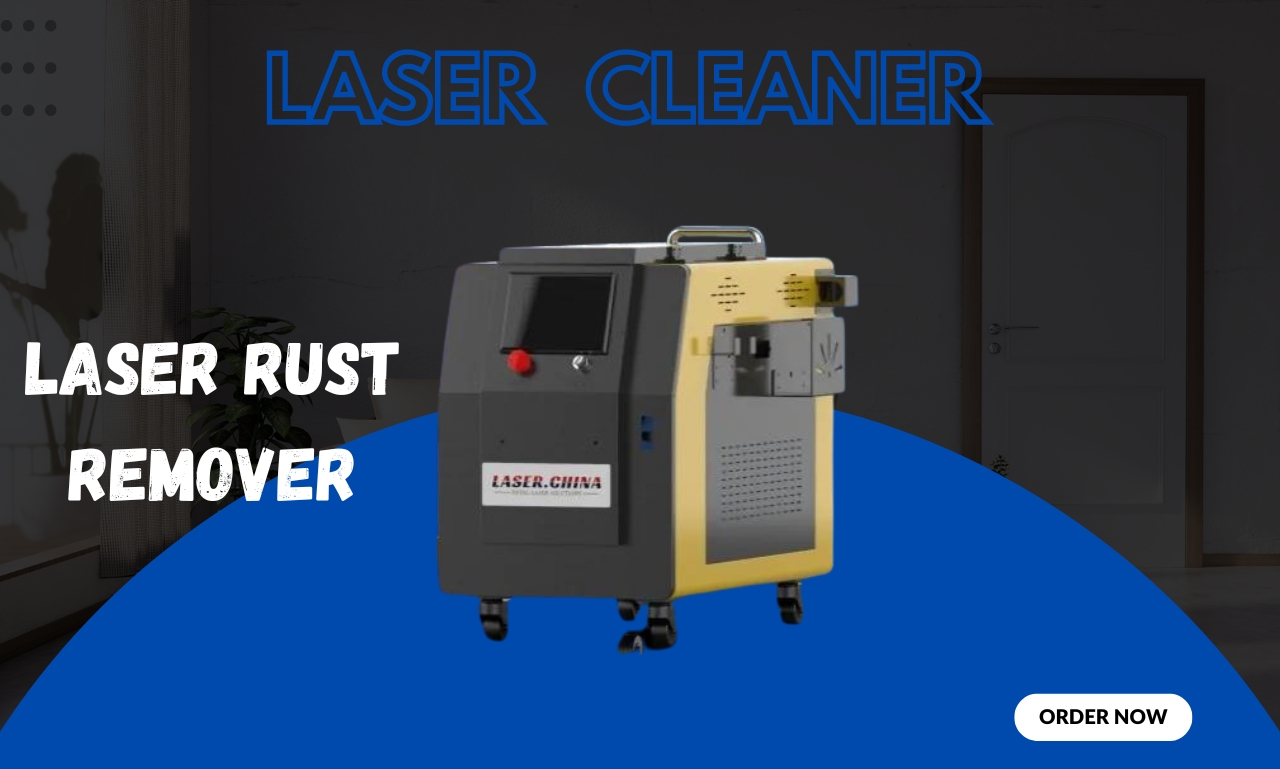
Handheld laser welders are revolutionizing the welding industry by offering precision, speed, and efficiency. Compared to traditional welding methods such as MIG, TIG, and arc welding, handheld laser welding provides numerous benefits, making it an ideal choice for industries requiring high-quality welds with minimal distortion. Here’s a comprehensive look at why handheld laser welders are becoming increasingly popular:
1. High Precision and Quality Welds
One of the biggest advantages of handheld laser welding is the precision it offers. The laser beam is highly focused, allowing for pinpoint accuracy when fusing metals. This results in clean, strong, and aesthetically pleasing welds with minimal heat-affected zones (HAZ). Unlike traditional welding, which can cause warping or excessive heat damage, laser welding ensures that materials maintain their integrity.
2. Increased Speed and Efficiency
Handheld laser welders operate at significantly higher speeds than conventional welding methods. Since the laser generates intense heat quickly, it can fuse metals much faster, reducing production time. This makes it an excellent choice for high-volume industries like automotive, aerospace, and manufacturing, where efficiency is crucial.
3. Minimal Material Distortion
Traditional welding generates excessive heat, which often leads to material warping, especially on thin metals. Handheld laser welders produce concentrated heat with minimal heat dispersion, reducing the risk of warping and material distortion. This makes them ideal for delicate and high-precision applications.
4. Versatility and Ease of Use
Unlike conventional welding, which requires extensive training and skill, handheld laser welding is user-friendly. Most laser welders come with intuitive interfaces and adjustable settings, making it easy for even less experienced operators to produce high-quality welds. Additionally, handheld laser welders can be used on various materials, including stainless steel, aluminum, titanium, and copper, without the need for frequent electrode changes.
5. Reduced Need for Post-Welding Processing
Traditional welding often requires extensive post-welding processing, such as grinding, polishing, and additional finishing work. Laser welding, however, produces smooth and clean welds with minimal spatter, reducing the need for additional refinishing. This saves both time and labor costs.
6. Improved Safety and Reduced Consumables
Traditional welding processes, such as MIG and TIG, require shielding gases, filler materials, and electrodes, which increase operational costs. Handheld laser welders reduce or eliminate the need for these consumables, making them cost-effective. Additionally, they generate less smoke and fewer toxic fumes, improving workplace safety for welders.
7. Portability and Convenience
Handheld laser welders are compact and lightweight compared to bulky traditional welding machines. Their portability allows for greater flexibility in various work environments, including hard-to-reach places or on-site repairs. This makes them an excellent tool for industries that require mobile welding solutions.
Conclusion
Handheld laser welders offer superior welding quality, faster processing times, and increased safety compared to traditional welding methods. Their precision, efficiency, and versatility make them a game-changer for industries that require high-quality welds with minimal heat damage. As technology continues to advance, handheld laser welding is expected to become even more efficient and widely adopted in various industrial applications.