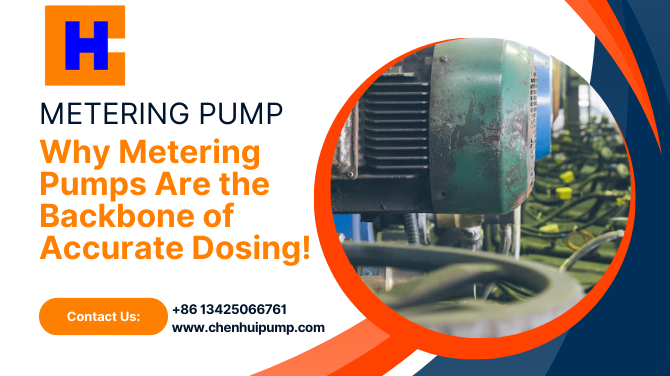
In today’s fast-paced industrial landscape, precision is non-negotiable, especially when it comes to dosing and fluid handling. Whether in the pharmaceutical, chemical, food and beverage, or water treatment industries, the ability to deliver exact quantities of liquids can mean the difference between success and failure. Metering pumps have risen to meet this challenge, becoming the backbone of accurate and reliable dosing systems across the globe.
Metering pumps are designed to provide a precise flow of liquids, ensuring that the exact dose is delivered every time. This ability is critical in industries where even a small variation in dosage can have a significant impact on the end product or process. For example, in pharmaceutical manufacturing, a slight discrepancy in drug formulation can result in substandard products, posing serious risks to health and safety. Similarly, in chemical processing, incorrect chemical dosing can lead to hazardous reactions or reduced product quality.
As the world moves towards automation and digitalization, the demand for precise fluid management has never been greater. Metering pumps are now being integrated into more sophisticated systems, allowing for real-time monitoring and adjustments, further enhancing the accuracy and efficiency of dosing applications.
What is a Metering Pump?
At its core, a metering pump is a positive displacement pump designed to deliver precise, adjustable volumes of liquid at specific intervals. This is crucial in applications where exact amounts of chemicals, additives, or other liquids need to be dispensed. These pumps can deliver accurate dosing over a wide range of flow rates and pressures, making them versatile for various applications.
The operation of a metering pump is based on a consistent mechanical movement or displacement. This ensures that each cycle of the pump moves a fixed amount of liquid. The flow rate of the pump can be adjusted manually or automatically, depending on the system requirements.
Metering pumps come in different types, including diaphragm, piston, and gear-driven pumps. Each type has its unique benefits, making it suitable for specific applications. Regardless of the type, all metering pumps share the same purpose: to provide precise fluid control.
Types of Metering Pumps
- Diaphragm Metering Pumps
Diaphragm pumps are perhaps the most common type of metering pump. They use a flexible diaphragm to move the liquid, ensuring that there is no contact between the liquid and the pump’s moving parts. This makes diaphragm pumps ideal for handling corrosive, toxic, or expensive liquids, as the diaphragm acts as a barrier between the fluid and the rest of the pump system. Diaphragm pumps are often used in water treatment, chemical processing, and pharmaceutical industries. - Piston Metering Pumps
Piston metering pumps use a piston to move the liquid through the pump. These pumps can generate higher pressures compared to diaphragm pumps, making them ideal
Applications of Metering Pumps
Metering pumps are incredibly versatile, used across a wide variety of industries. They are relied upon to maintain the highest levels of precision in diverse environments, and their adaptability is one of their most significant features. Let’s dive into the main sectors where metering pumps are making a substantial impact.
1. Pharmaceuticals and Healthcare
The pharmaceutical industry demands the highest level of precision and reliability in its manufacturing processes. Metering pumps are used extensively in the preparation of pharmaceutical formulations, including in the production of injectable medications and syrups. The accuracy of the metering pump ensures that the right quantity of active pharmaceutical ingredients (APIs) is delivered into the formulation, thereby maintaining consistency and efficacy.
The pumps are also employed in the dosing of various excipients, stabilizers, and preservatives, which are vital for drug stability and shelf life. A minor error in dosing can have significant consequences, not only affecting the quality of the product but also compromising patient safety.
2. Water and Wastewater Treatment
Metering pumps are critical in water and wastewater treatment facilities, where chemicals such as chlorine, coagulants, and flocculants need to be added to purify water. These chemicals need to be dosed at very precise rates to ensure the water is treated effectively and safely, without wasting resources or endangering public health.
Furthermore, in sewage treatment, metering pumps are used to ensure that the right chemicals are used for disinfecting the water, adjusting pH levels, or eliminating harmful bacteria. The ability to automate these processes and make real-time adjustments has greatly improved the efficiency of water treatment plants worldwide.
3. Chemical Industry
The chemical industry is perhaps one of the most critical areas for metering pumps. From the production of industrial chemicals to the formulation of agricultural pesticides, precise dosing is key to producing quality products and maintaining safety.
Chemicals often react in highly sensitive ways, and metering pumps are designed to deliver exact quantities of chemicals to prevent unwanted reactions or variations in product quality. Whether handling high-viscosity liquids, volatile substances, or corrosive materials, metering pumps offer safe and reliable operation.
4. Food and Beverage Processing
In food and beverage processing, metering pumps are essential for ensuring that ingredients like flavorings, preservatives, and colorings are added in the exact quantities required. These pumps are designed to handle a wide range of viscosities, making them ideal for liquids, slurries, and even highly viscous substances like syrups or oils.
The precise dosing offered by metering pumps ensures that the end product is consistent, safe, and meets all regulatory requirements. From dairy products to beverages, from condiments to packaged meals, metering pumps help manufacturers maintain the quality and taste that consumers expect.
5. Oil and Gas Industry
The oil and gas industry involves the handling of large volumes of fluids, including fuels, lubricants, and chemicals. Metering pumps are used to accurately dose these fluids for a variety of purposes, including chemical injection for oil recovery, fuel transfer, and lubricating systems.
In this industry, the ability to deliver precise amounts of fluid is critical for maximizing efficiency, reducing waste, and maintaining the safety of operations. Metering pumps help ensure that the correct amounts of fluid are dispensed, contributing to smooth and safe processes.
How to Choose the Right Metering Pump for Your Application?
Choosing the right metering pump for your application requires careful consideration of several factors. Here are some key aspects to keep in mind:
1. Flow Rate
One of the first things to consider when selecting a metering pump is the required flow rate. Different pumps can handle different flow ranges, so understanding the specific needs of your process is essential. For low-flow applications, you may require a more precise pump, while high-flow applications may demand a more robust system.
2. Pressure Requirements
Metering pumps also vary in terms of the pressures they can handle. Some applications may require pumps capable of working under high pressure, especially in industries like oil and gas. Others may require lower-pressure systems for more delicate applications like pharmaceuticals or food production.
3. Fluid Type
Different metering pumps are suited for different types of fluids. For instance, some pumps are designed to handle high-viscosity liquids, while others are better equipped for handling volatile, corrosive, or abrasive fluids. Consider the characteristics of the fluid you’re working with to determine which pump is the best fit.
4. Precision and Control Features
Metering pumps come with various levels of precision, and some offer advanced control systems for real-time monitoring and adjustments. If your application requires very precise dosing, look for a pump that allows for fine adjustments and offers reliable accuracy. Many modern metering pumps include digital controllers and automated feedback systems that help maintain dosing accuracy.
5. Durability and Maintenance
Consider the long-term durability of the pump, especially if it will be operating in demanding environments. Pumps used in harsh conditions, such as chemical processing or oil and gas applications, should be constructed from corrosion-resistant materials and have a long service life. Additionally, consider the ease of maintenance, as regular upkeep is essential to ensuring continued pump performance.
Metering Pump Innovations and Future Trends
As industries continue to evolve, so do the technologies that support them. The metering pump industry is not standing still—innovations continue to drive improvements in performance, efficiency, and integration.
1. Smart Metering Pumps
With the rise of the Internet of Things (IoT) and Industry 4.0, smart metering pumps are becoming increasingly common. These pumps feature integrated sensors, real-time monitoring, and remote control capabilities, allowing operators to manage and adjust dosing systems from anywhere in the world. The integration of smart sensors helps ensure precise operation, reduce downtime, and minimize human error.
2. Energy-Efficient Designs
Energy efficiency is a growing concern across all industries, and metering pumps are no exception. Manufacturers are designing more energy-efficient pumps to help reduce energy consumption and lower operational costs. These pumps not only save money but also contribute to more sustainable operations.
3. Automation Integration
Automation is at the forefront of modern industrial processes, and metering pumps are no different. Advanced control systems are now more seamlessly integrated into automated manufacturing environments, allowing for better synchronization between production lines, quality control, and dosing systems.
Metering pumps are truly the backbone of accurate dosing across industries, offering precision, efficiency, and reliability. From pharmaceuticals to food production, water treatment to oil and gas, these pumps play a vital role in ensuring that the right amount of fluid is dispensed, time after time.
With innovations in automation, smart technologies, and energy-efficient designs, the metering pump industry is poised to continue growing and evolving. Businesses that rely on accurate fluid dosing can benefit from the continued advancement of metering pump technology, making their processes more efficient, safe, and cost-effective.
For those looking to implement or upgrade their dosing systems, understanding the different types of metering pumps and their applications is crucial. With the right choice of metering pump, businesses can ensure precision in every drop, supporting high-quality production and maximizing efficiency.

FAQs
1. What is the difference between a metering pump and a regular pump?
A metering pump delivers a precise, adjustable volume of liquid with each cycle, making it ideal for applications that require accurate dosing. In contrast, regular pumps may not offer the same level of precision and are typically used for general fluid transport.
2. Can metering pumps handle all types of fluids?
Metering pumps are designed to handle a wide variety of fluids, including corrosive, viscous, and shear-sensitive liquids. However, it’s important to choose a pump suited to the specific characteristics of the fluid you are working with.
3. How do I adjust the flow rate of a metering pump?
Many modern metering pumps feature adjustable control systems, allowing operators to fine-tune the flow rate. Some pumps can also be integrated into automated systems for real-time adjustments based on factors like pressure and volume.
4. What industries use metering pumps?
Metering pumps are used in industries such as pharmaceuticals, chemicals, food and beverage, water treatment, oil and gas, and many others where precise dosing is essential.
5. How often should metering pumps be maintained?
Metering pumps should be regularly maintained to ensure optimal performance. The frequency of maintenance depends on the application and the pump’s operating conditions, but it’s generally recommended to inspect the pump at least every six months.