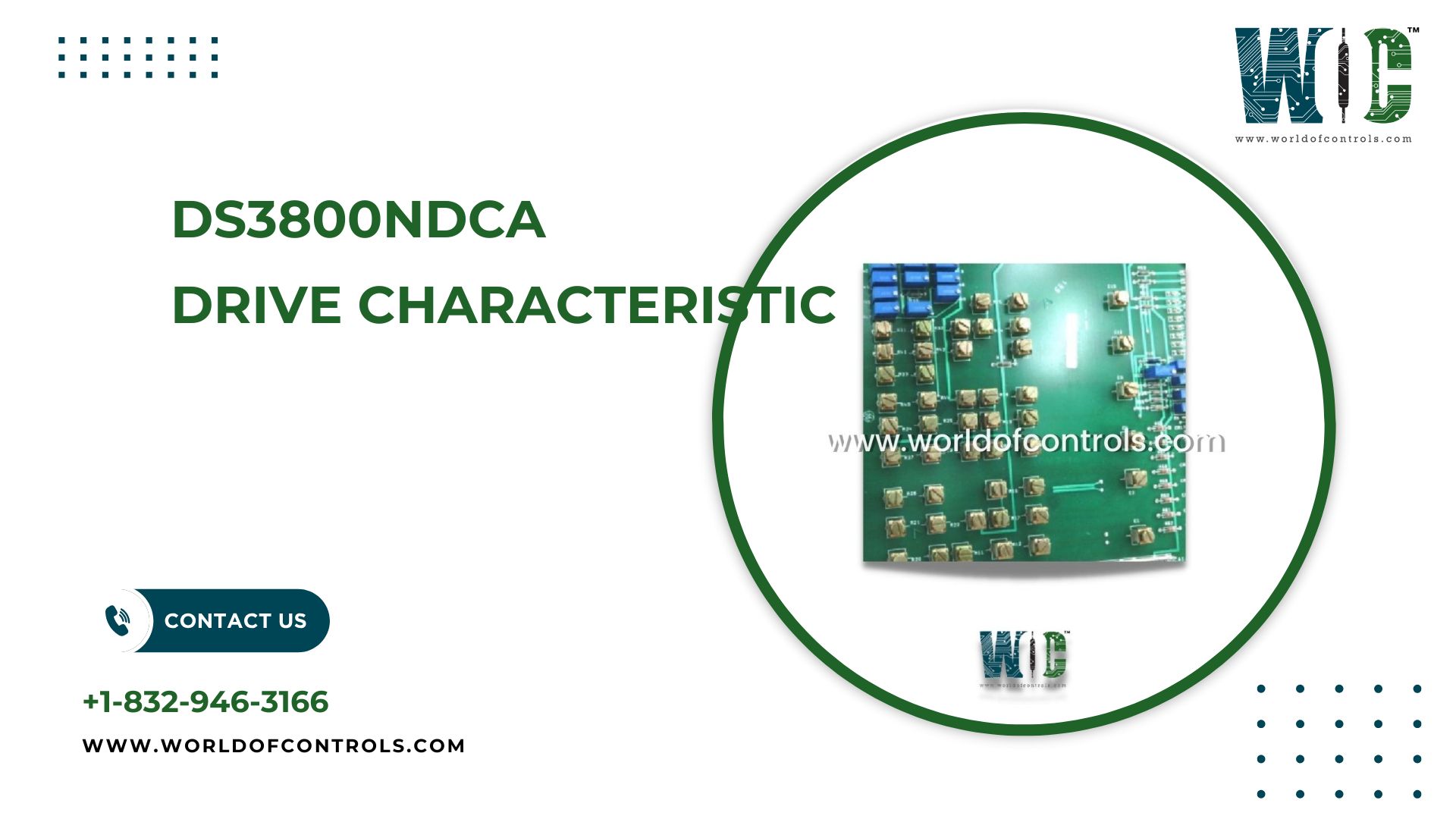
Introduction
In the high-demand world of industrial power generation, particularly in gas and steam turbines, the precision and reliability of every control component are essential. One critical element in this system is the drive control module—a specialized circuit board that manages the operation of motors and drives that power auxiliary and core turbine functions. To guarantee the best possible performance, safety, and longevity of turbine systems, it is essential to comprehend the features of these modules.
What is a Drive Control Module?
A drive control module is an electronic board that regulates motor functions such as speed, torque, direction, and timing. In turbine environments, these modules serve as the brain behind actuator movements, fuel valve positioning, and various mechanical operations. They interface with sensors, processing units, and feedback systems to execute real-time adjustments based on turbine load, temperature, and pressure readings.
Importance in Turbine Control Systems
A network of interconnected modules is a key component of contemporary turbine control topologies, such GE’s Speedtronic systems. The drive control module plays a pivotal role in this setup, acting as both a signal interpreter and actuator manager. Its main tasks include:
1. Motor Speed and Torque Regulation
It ensures that motors operate within their designed parameters, which is critical for functions like fuel injection timing and variable guide vane control.
2. System Coordination
It works in harmony with other control boards to maintain timing and sequence integrity. This ensures proper startup, shutdown, and load transfer procedures.
3. Real-Time Response
Through advanced signal processing and feedback integration, the module makes near-instantaneous adjustments, which is vital in avoiding performance fluctuations and maintaining output consistency.
Core Drive Characteristics
To function effectively in turbine systems, a drive control module must exhibit several essential characteristics:
High Precision
Drive control modules must handle both analog and digital signals with high accuracy. Even minor miscalculations in motor command signals can lead to mechanical inefficiencies or operational risks.
Robust Environmental Tolerance
Turbine environments expose control electronics to significant heat, vibration, and electrical noise. A reliable drive module is designed with components that tolerate high temperatures, power fluctuations, and electromagnetic interference.
Feedback Integration
A key feature of these modules is their ability to operate within closed-loop systems, where feedback from sensors is used to adjust output dynamically. This ensures that motor behavior stays aligned with system goals even as external conditions change.
Common Applications in Turbine Systems
Drive control modules are commonly used in:
-
Fuel valve actuation
-
Compressor inlet guide vane adjustment
-
Hydraulic and pneumatic actuator management
-
Auxiliary system drives, such as cooling fans or oil pumps
These functions directly impact efficiency, emissions control, and safety. Reliable module performance leads to reduced downtime and increased operational lifespan.
Maintenance and Reliability
In power generation facilities, reliability is paramount. Drive control modules are typically modular and field-replaceable, allowing for quick maintenance with minimal disruption. Regular testing, cleaning, and thermal inspections can extend the lifespan of the module. Many operators keep spare units on hand, especially for legacy systems, to avoid prolonged outages.
Final Thoughts
Drive control modules are foundational to modern turbine automation. Their characteristics—ranging from signal accuracy and environmental resilience to real-time control—directly influence turbine efficiency and safety. Whether you’re managing a large-scale power plant or maintaining industrial automation systems, understanding the characteristics and capabilities of these modules is critical for success.