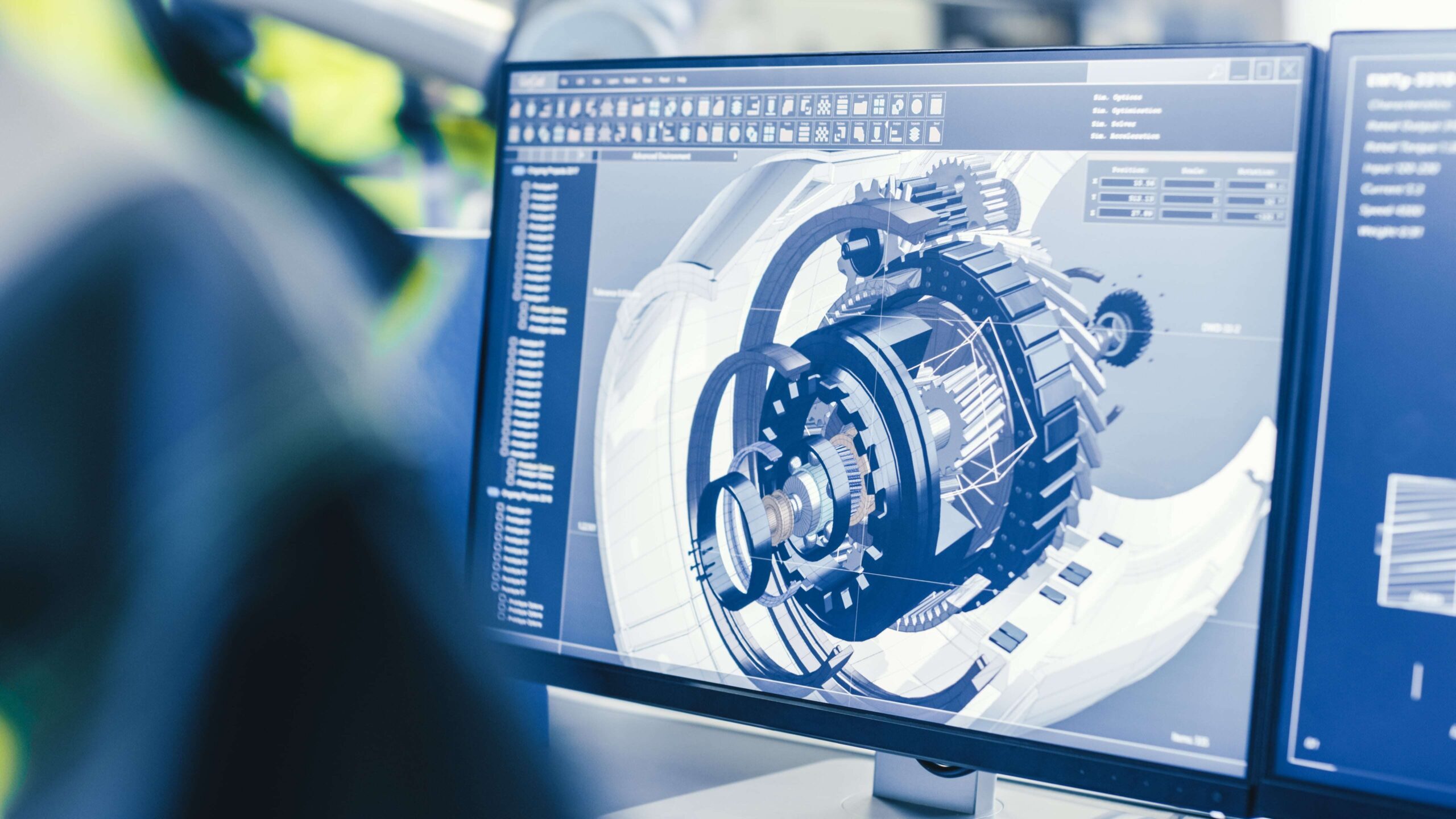
Producing intricate aircraft fasteners depends on precision machining, hence Swiss machining centers lead front stage in this technical development. Originally designed for small watch component manufacture, Swiss-style lathes have matured into sophisticated machines competent of ultra-precise, high- volume manufacturing of intricate parts.
Extreme accuracy and minimum deflection are made possible by a Swiss machining center, which runs with the workpiece maintained rather near to the cutting tool under a guiding bushing. In aircraft production, where components can need for exact tolerances and complex geometry, this is very helpful.
Advantages of Swiss machining centers for manufacture of aerospace fasteners:
Important for safety-critical aerospace applications, tight tolerances allow one to retain dimensional precision within microns.
Fasteners with threads, grooves, undercuts, and other complicated elements may be created in a single setup using simple geometries.
Important for certification and compliance in aircraft manufacturing, high repeatability guarantees consistency between manufacturing runs.
Aerospace-grade materials like titanium, Inconel, stainless steel, and aluminum alloys are within your grasp.
Efficiency: By finishing items in one cycle, ancillary procedures are cut down, therefore accelerating manufacturing times.
These features make Swiss machining centers a great resource in making specialized fasteners that satisfy the needs of legacy aircraft and next-generation platforms including electric vertical takeoff and landing (eVTOL) aircraft, unmanned aerial vehicles (UAVs), and supersonic jets.
Quick Turn CNC Machining: Accuracy Meets Velocity
Apart from the features of Swiss machining, the aerospace sector is depending more and more on quick turn CNC machining services to speed up development cycles and meet rapidly changing needs. Quick turn CNC machining lets manufacturers create high-precision bespoke fasteners in days rather than weeks, whether for rapid prototype or urgent replacement components.
In manufacturing of aircraft fasteners, rapid turn CNC machining enhances Swiss machining in the following ways:
Rapid Prototyping: During the R&D stage, engineers may rapidly evaluate many fastener designs, therefore enhancing performance and lowering the time to market.
Helps handle supply chain interruptions or unanticipated demand for certain components via on-demand manufacturing.
For specialized aviation components, customizing makes rapid, low-volume runs of original or modified fasteners possible.
Integration of CAD/CAM systems with CNC machines helps to produce seamlessly depending on digital models.
Quick turn CNC machining is a critical tool for being competitive and responsive in the aerospace industry as aircraft designs become more complicated and development schedules are squeezed.
The Evolution of Aerospace Design: Fresh Problems for Fasteners
Driven by new concerns like sustainability, performance, and automation, aircraft designs are undergoing radical change. These changes bring new fastening needs.
Lightweighting: Lightweight metals and carbon composites are replacing conventional materials. Fasteners must match these substrates both mechanically and chemically.
Fasteners used in modular aircraft components must allow for simpler disassembly and reassembly while also preserving structural integrity.
Next-generation propulsion systems—such as hypersonic engines—need fasteners able to survive significant temperature cycles.
As components become smaller—especially in avionics and drones—smaller fasteners with better strength-to—-sized ratios are required.
Standard fasteners make it difficult to meet these criteria, hence manufacturers are driven to use innovative machining techniques and materials in order to create custom fastening solutions.
Materials Matter: Choosing Correct Alloy
In fastener manufacture, material choice is very important as it affects performance qualities like strength, corrosion resistance, thermal expansion, and fatigue life. Custom aircraft fasteners are often made from:
Perfect for major aeronautical components, titanium is lightweight, robust, and corrosion-resistant.
High temperature and corrosion resistance nickel-chromium-based superalloys, inconel
Often employed throughout aviation systems, stainless steel provides a compromise of strength and corrosion resistance.
Lightweight and easily machined aluminum alloys are utilized when little strength is acceptable.
When combined with rapid turn CNC machining, producers may effectively make fasteners that are not only high-performance but also customized to the demands of the application as Swiss machining centers can handle all these materials with accuracy.
Thoughts on Regulatory and Quality Assurance
Manufacturing aircraft fasteners calls for compliance as much as performance. Every fastener has to satisfy exacting criteria established by aerospace OEMs, EASA, and aviation regulators like the FAA.
Among important certifications and standards are AS9100 Certification: Quality Management System Standard for Aerospace Industry.
Coverage for unique procedures including chemical processing and heat treatment under NADCAP Accreditation
Every fastener has to be traceable from its original raw material source.
Non-destructive testing (NDT) guarantees structural integrity free from component damage.
Swiss machining centers and CNC machines fitted with in-process inspection and monitoring systems assist to guarantee that every fastener meets these exacting quality standards.
In summary, innovation meets accuracy.
Though their influence on safety, performance, and innovation is great, custom fasteners look like little parts in the big picture of aircraft building. Technologies such as fast turn CNC machining and the Swiss machining center help aerospace producers to be more suited than ever to satisfy the needs of contemporary aircraft design.
Whether it’s flying higher, faster, or greener—as aircraft design pushes the boundaries of what’s possible—the fasteners keeping it all together must change in concert. Companies can guarantee they remain aloft in a very competitive and fast-moving sector by investing in precise machining skills and agile production techniques.