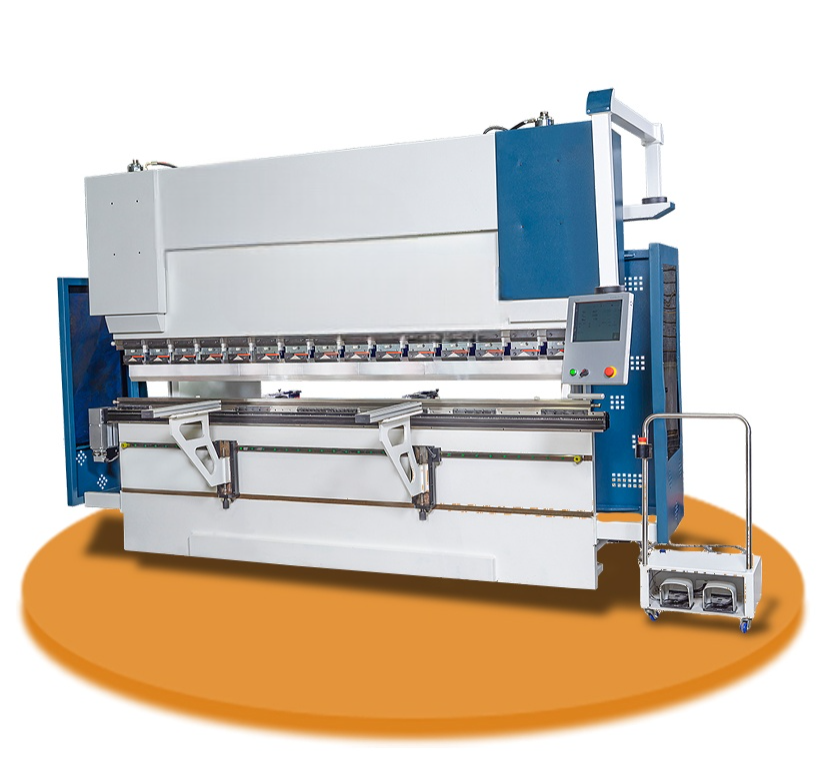
In the world of metal fabrication, Press Brake Machine Manufacturers play a critical role in delivering precision, durability, and high-performance machines. These manufacturers are responsible for engineering the backbone of countless industrial processes—from automotive production to aerospace fabrication. To meet the ever-evolving needs of global industries, quality has become the hallmark of leading Press Brake Machine Manufacturers.
Let’s explore how top-tier manufacturers ensure consistent quality, retain industry trust, and maintain leadership in a competitive market.
Understanding Press Brake Machines and Their Industrial Relevance
A press brake machine is a powerful tool used to bend sheet metal into various forms. It is a staple in manufacturing workshops, known for its precision and ability to handle complex metal bending tasks. Whether it’s a hydraulic, mechanical, or CNC press brake, each version demands high standards of accuracy and reliability.
In industries where precision is non-negotiable, the quality of a press brake machine determines productivity, product consistency, and operational safety. That’s why Press Brake Machine Manufacturers must align their processes with international quality benchmarks.
Key Strategies Leading Manufacturers Use to Ensure Quality
1. Advanced Design and Engineering
Top Press Brake Machine Manufacturers begin their quality journey with robust design and engineering. They utilize advanced 3D CAD software and simulation tools to analyze stress points, structural durability, and load capacity before production.
Some manufacturers even use finite element analysis (FEA) to predict machine behavior under real-world conditions—ensuring the final product delivers uncompromising performance.
2. Premium Material Selection
Quality starts with raw materials. Leading Workshop Machines Manufacturers, who often also produce press brakes, ensure that the steel, electronics, and hydraulic components are sourced from verified suppliers with proven quality records.
Using high-grade materials minimizes wear and tear, extends machine lifespan, and boosts performance reliability.
3. Precision Manufacturing Processes
Accuracy in manufacturing is vital. Reputable Press Brake Machine Manufacturers use state-of-the-art CNC machining centers, laser cutting systems, and robotic welding technologies to achieve micron-level precision.
Notable Practices:
· Laser calibration for component alignment
· In-house machining for tighter quality control
· Multi-stage inspections during fabrication
4. Stringent Quality Control Measures
Every stage of production—design, machining, assembly, and testing—is subjected to rigorous quality control checks.
Tools Used:
· Coordinate Measuring Machines (CMM)
· Ultrasonic flaw detectors
· Surface hardness testers
These systems help identify microscopic defects that can impact long-term performance.
Testing and Certification: Non-Negotiable Quality Aspects
1. Load Testing and Trial Runs
Before delivery, leading Workshop Machines Manufacturers conduct load testing and live trial runs to validate the machine’s performance under operational conditions. This ensures the machine’s real-world capability matches its technical specifications.
2. Compliance with International Standards
Credible Press Brake Machine Manufacturers design their machines in compliance with international standards such as:
· ISO 9001 (Quality Management Systems)
· CE Marking (European Conformity)
· ANSI/ASME (for North American markets)
These certifications signal a manufacturer’s commitment to delivering globally accepted quality.
How Manufacturers Maintain Consistent Quality Post-Sale
1. Comprehensive Training and Documentation
Top manufacturers not only provide installation and training but also share detailed user manuals, safety guidelines, and maintenance schedules. This empowers the client’s team to operate the machine safely and efficiently.
2. Responsive After-Sales Support
Being among the best Press Brake Machine Manufacturers means offering round-the-clock support, replacement part availability, and remote diagnostics. Quick support reduces downtime and protects the client’s investment.
Role of Digital Transformation in Quality Assurance
1. Smart Monitoring Systems
Modern press brakes are equipped with sensors and IoT systems that continuously monitor performance. These smart systems detect inefficiencies and trigger alerts, allowing manufacturers to take preventive actions.
2. Data-Driven Improvements
Leading Workshop Machines Manufacturers collect performance data from deployed machines. This data helps them make informed decisions to refine future machine designs, ensuring continuous improvement and innovation.
Case Study: How a Leading Manufacturer Ensures Excellence
Let’s consider a renowned name in the Press Brake Machine Manufacturers industry. This company has implemented the following to assure world-class quality:
· Developed an in-house R&D lab for testing new designs
· Partnered with global material suppliers for consistent input quality
· Achieved multiple ISO certifications
· Installed AI-based inspection systems
· Offers a 24/7 support model for international clients
Such practices exemplify why the company is not only a top Press Brake Machine Manufacturer but also a respected name among Workshop Machines Manufacturers worldwide.
Why It Pays to Choose the Right Manufacturer
Selecting from among the leading Press Brake Machine Manufacturers offers long-term benefits such as:
· Reduced machine downtime
· Lower maintenance costs
· Enhanced product quality in your own operations
· Reliable technical support
· Scalable integration with other Workshop Machines Manufacturers
Conclusion
In today’s competitive industrial landscape, quality is no longer optional—it’s a prerequisite. Leading Press Brake Machine Manufacturers invest in cutting-edge technology, implement strict quality control protocols, and prioritize customer support to maintain their status in the market. Likewise, top Workshop Machines Manufacturers set high standards that influence every aspect of machine production and usage.
By choosing a quality-focused manufacturer, businesses not only ensure the longevity of their machinery but also boost their overall operational efficiency. Always prioritize those who make quality their mission, not just a metric.