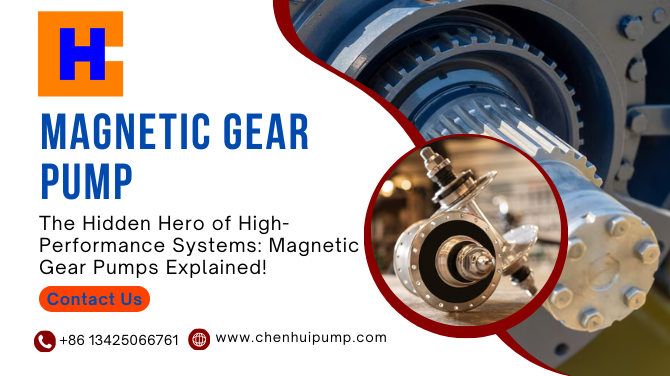
In the fast-paced world of advanced machinery and high-performance engineering, certain components quietly perform critical roles behind the scenes. While the spotlight often falls on complex engines, cutting-edge electronics, or automated software systems, there’s one unsung hero that deserves far more recognition — the Magnetic Gear Pump. At Zhuhai Chenhui Technology Co., LTD, we believe in shining a light on the technology that powers excellence. And when it comes to consistent, reliable, and contamination-free fluid handling, magnetic gear pumps are leading the charge.
Magnetic gear pumps offer a unique combination of sealing integrity, fluid accuracy, and high reliability in applications where performance cannot be compromised. From chemical processing plants to pharmaceutical laboratories, and from aerospace engineering to semiconductor manufacturing, magnetic gear pumps serve as the backbone of fluid transfer systems that demand the highest level of control and durability.
As their name suggests, these pumps utilize magnetic coupling instead of direct mechanical connection between the motor and the gear assembly. This seemingly small innovation leads to massive advantages — especially in terms of leak-proof operation, maintenance reduction, and improved system longevity. Moreover, the absence of a traditional shaft seal eliminates one of the most common failure points in conventional pumps, making magnetic gear pumps ideal for transporting corrosive, toxic, or ultra-pure fluids.
In fact, the demand for magnetic gear pumps has surged in recent years. This growing interest is not just a trend — it’s a response to increasingly stringent performance and safety requirements across multiple industries. Companies are realizing that investing in the right pump technology doesn’t just enhance efficiency; it safeguards product quality, reduces downtime, and ultimately, cuts costs.
What is a Magnetic Gear Pump?
A magnetic gear pump is a positive displacement pump that uses magnets to transfer torque from a motor to a pump rotor without direct mechanical contact. This innovation eliminates the need for traditional shaft seals — a common source of leaks in conventional pumps — making it ideal for handling hazardous, volatile, or ultra-pure fluids.
Magnetic vs Traditional Gear Pumps
While traditional gear pumps use a shaft to connect the motor to the gears, magnetic gear pumps replace that with a magnetic coupling system. This design separates the drive and pump chambers with a containment shell, isolating the fluid and providing a seal-less, leak-proof solution.
Components and Construction
Magnetic gear pumps typically consist of:
- An outer magnet rotor attached to the motor
- An inner magnet rotor connected to the pump gears
- A containment shell separating the two
- Precision gears (spur or helical) for fluid displacement
This simple yet brilliant construction makes them perfect for situations where clean operation and zero emissions are crucial.
How Does a Magnetic Gear Pump Work?
- The Principle of Magnetic Coupling
The outer magnetic rotor rotates when the motor is powered. Through magnetic attraction, it drives the inner rotor, which is located inside the sealed pump chamber. This magnetic coupling allows torque to transfer across the containment shell without any physical contact. - Internal Gear Motion and Flow Path
As the gears rotate, they trap fluid between the gear teeth and the pump housing, transporting it from the inlet to the outlet in a smooth, controlled flow. This positive displacement mechanism ensures high accuracy, especially in dosing or metering applications. - Seal-less Operation Advantage
Because there are no mechanical seals exposed to the pumped fluid, the risk of leaks, contamination, or failure is significantly reduced. This is particularly valuable when handling acids, solvents, or flammable liquids.
Key Benefits of Magnetic Gear Pumps
- Leak-Free Design
With no shaft seal to worry about, magnetic gear pumps are completely leak-tight, making them ideal for industries where safety and cleanliness are non-negotiable. - Chemical and Corrosion Resistance
Constructed with high-grade materials like PTFE, stainless steel, or ceramics, these pumps resist corrosion even when exposed to aggressive chemicals. - Low Maintenance Needs
Fewer moving parts mean fewer wear points. Magnetic gear pumps often require minimal maintenance, reducing both labor and operational costs. - High Precision and Efficiency
These pumps offer precise volumetric flow rates, making them ideal for metering, dosing, or microfluidic systems. - Noise and Vibration Reduction
Because there’s no mechanical contact between motor and pump, operation is smoother and quieter, reducing stress on connected systems.
Applications Across Industries
- Chemical and Petrochemical Plants
Used for safely transferring corrosive acids, solvents, and reactive agents, magnetic gear pumps excel in environments where sealing integrity is critical. - Pharmaceutical and Biotech
With their sanitary design and accurate flow rates, these pumps are ideal for handling sterile solutions, nutraceuticals, and active pharmaceutical ingredients (APIs). - Food and Beverage Processing
They ensure hygienic, contamination-free transfer of flavorings, oils, or syrups, supporting FDA compliance and clean-in-place (CIP) processes. - Semiconductor and Electronics
Used to pump ultra-pure chemicals in chip manufacturing and etching processes, where zero contamination is vital. - Aerospace and Automotive
From fuel systems to lubricant circulation, magnetic gear pumps help maintain high performance under extreme conditions.
Magnetic Gear Pump vs Traditional Gear Pumps
- Efficiency and Reliability
When it comes to operational efficiency, magnetic gear pumps outperform their traditional counterparts in several key areas. Thanks to their leak-proof design and smooth torque transmission, they offer more consistent flow rates, better energy conservation, and fewer mechanical issues. Without seals or direct coupling mechanisms, wear and tear are drastically reduced, resulting in improved reliability and longevity. - Durability Under Harsh Conditions
In challenging environments—such as high-temperature or corrosive fluid applications—traditional gear pumps often fail due to seal degradation. Magnetic gear pumps, on the other hand, can withstand extreme conditions due to their non-contact design and corrosion-resistant materials, ensuring reliable performance even under the most demanding circumstances. - Long-Term Operational Costs
Although the initial cost of a magnetic gear pump might be slightly higher, the reduction in maintenance, downtime, and replacement parts makes it a more cost-effective choice in the long run. Industries that switch to magnetic gear pumps often report a significant decrease in total cost of ownership (TCO) over time.
Choosing the Right Magnetic Gear Pump
- Key Selection Factors
Choosing the ideal magnetic gear pump for your system requires careful consideration. Factors such as fluid type, viscosity, temperature, required flow rate, and pressure must be evaluated. Moreover, you must ensure the selected materials are chemically compatible with your media. - Understanding Your Fluid Requirements
For aggressive or volatile chemicals, you may require a pump built with PTFE linings, Hastelloy components, or ceramic bushings. If you’re pumping delicate fluids in pharmaceutical or food applications, material purity and hygiene standards will be paramount. - Capacity, Flow Rate, and Pressure Ratings
Magnetic gear pumps are highly customizable in terms of size, RPM, and performance parameters. Whether you need micro-dosing or bulk fluid transfer, selecting the appropriate configuration will ensure optimal system integration and performance.
Installation and Maintenance Tips
Best Practices for Setup
To maximize the life and efficiency of a magnetic gear pump:
- Ensure proper alignment between the motor and magnetic coupling
- Use vibration-dampening mounts where necessary
- Avoid dry running, which could damage internal gears
- Implement fluid filtration systems to prevent debris from entering the pump chamber
Preventive Maintenance Guidelines
Although magnetic gear pumps are low-maintenance, periodic inspection is still advised:
- Check magnet alignment and wear
- Inspect bearings and bushings
- Clean internal components as needed (especially in sticky or residue-prone applications)
Common Troubleshooting Tips
- Inconsistent flow? Check for air in the system or blocked inlets.
- Noise or vibration? May indicate magnet misalignment or cavitation.
- Overheating? Ensure proper cooling and that fluid viscosity is within recommended limits.
Zhuhai Chenhui Technology Co., LTD – Industry Leader
- Company Overview
With years of experience and innovation, Zhuhai Chenhui Technology Co., LTD has earned a reputation as a pioneer in fluid dynamics solutions. Specializing in magnetic gear pump technology, the company delivers products that meet the highest international standards in safety, performance, and sustainability. - Product Innovations and R&D
The company’s state-of-the-art R&D team focuses on continuous improvement, ensuring each magnetic gear pump is designed for precision and durability. From small-capacity micro pumps to heavy-duty industrial models, their catalog serves a wide range of global industries. - Commitment to Quality and Customization
Zhuhai Chenhui Technology Co., LTD is proud to offer custom-built magnetic gear pumps, tailored to client specifications. Their commitment to ISO-certified production, thorough quality assurance, and technical support makes them a preferred supplier across various sectors. - Sustainability and Eco-Efficiency
Reducing Waste and Spillage
One of the major advantages of using magnetic gear pumps is their ability to eliminate product loss through leaks or spillage. This is especially critical in industries handling expensive or hazardous fluids. - Energy-Efficient Designs
Due to the low-friction operation and optimized gear systems, magnetic gear pumps consume less energy compared to other pump types. This translates into lower carbon footprints and reduced operational costs. - Long Lifecycle Benefits
Durable components, combined with low maintenance needs, result in a longer operational life. This not only improves ROI but also aligns with corporate sustainability goals by reducing the need for frequent replacements.
Real-World Case Studies
Successful Installations
Across Asia, Europe, and North America, Zhuhai Chenhui Technology Co., LTD has successfully deployed magnetic gear pumps in various high-stakes environments:
- Semiconductor manufacturing lines
- Chemical processing plants
- Bio-pharmaceutical production facilities
Each installation has demonstrated improved safety, increased productivity, and reduced system downtime.
Measurable Performance Improvements
Clients have reported:
- Up to 40% reduction in maintenance hours
- 30% energy savings compared to conventional pumps
- Near-zero leakage incidents, enhancing plant safety and compliance
Client Testimonials
One client in the chemical industry shared:
“After switching to magnetic gear pumps from Zhuhai Chenhui, we’ve completely eliminated leakage problems. The precision and consistency have helped us reduce waste and improve batch quality significantly.”
The Future of Magnetic Gear Pumps
- Smart Monitoring and IoT Integration
The next frontier involves smart magnetic gear pumps equipped with real-time sensors and remote diagnostics. These innovations will allow users to monitor performance, predict failures, and automate maintenance schedules. - Material Advancements
Ongoing research is improving material strength, thermal resistance, and chemical compatibility—making magnetic gear pumps even more versatile. - Growing Global Demand
As more industries prioritize safety, efficiency, and sustainability, magnetic gear pumps will become integral components in smart factories, green energy systems, and next-gen manufacturing.
From chemical precision to pharmaceutical purity, the magnetic gear pump is the unsung hero powering many of today’s most advanced technologies. Its leak-proof, energy-efficient, and highly customizable design makes it an indispensable tool in countless industries.
Zhuhai Chenhui Technology Co., LTD continues to lead the way, offering cutting-edge magnetic gear pump solutions that meet the needs of a rapidly evolving world. As industries move towards smarter, safer, and more sustainable operations, magnetic gear pumps will only become more central to high-performance systems.
FAQs
Q1: What fluids can be used with a magnetic gear pump?
A: Magnetic gear pumps are suitable for a wide range of fluids including corrosive chemicals, acids, solvents, fuels, and even food-grade liquids, depending on material compatibility.
Q2: How long does a magnetic gear pump typically last?
A: With proper usage and maintenance, a magnetic gear pump can last several years, often outlasting traditional pumps by a significant margin.
Q3: Are magnetic gear pumps safe for explosive environments?
A: Yes. Their seal-less design reduces the risk of leaks and sparks, making them a safer option for handling flammable or volatile substances.
Q4: Can magnetic gear pumps be customized for specific needs?
A: Absolutely. Zhuhai Chenhui Technology Co., LTD offers custom-built solutions to meet specific flow rates, pressures, and material requirements.
Q5: What industries benefit most from magnetic gear pumps?
A: Industries such as chemical processing, biotech, food and beverage, semiconductor manufacturing, and aerospace benefit significantly from using magnetic gear pumps due to their precision and reliability.