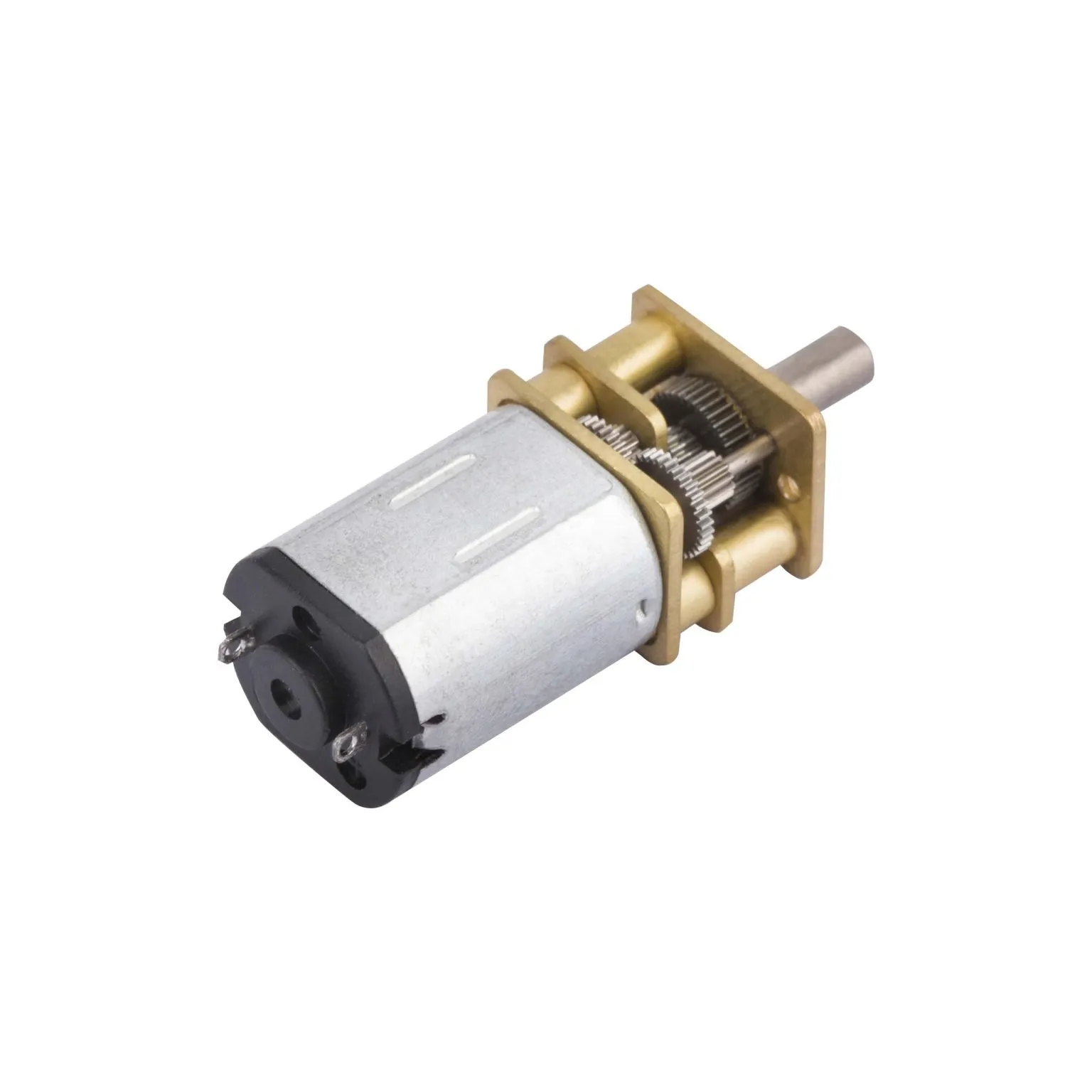
When choosing the right motor for your application, understanding the differences between a DC gear motor and a standard DC motor is essential. Both devices convert electrical energy into mechanical motion, but they serve different purposes and deliver unique performance characteristics. This article explores the key differences between these two motor types, highlighting why a DC gear motor might be the better choice for certain projects. We will also introduce how Kinmore Motor, a trusted industry brand, offers solutions that leverage these differences for maximum efficiency.
What Is a Standard DC Motor?
A standard DC motor is an electric motor that runs on direct current (DC) electricity. It works by converting electrical energy into rotational mechanical energy. The motor’s core components include the rotor, stator, brushes, and commutator. When electricity passes through the motor’s windings, it creates a magnetic field that interacts with magnets, causing the rotor to turn.
Standard DC motors offer several advantages:
- Simple design and construction
- Easy speed control by varying voltage
- Reliable and efficient for many applications
- Compact and lightweight
However, these motors tend to operate at high speeds with relatively low torque. For many applications, such as conveyor belts or small fans, this speed is ideal. But for projects requiring higher torque at lower speeds, a standard DC motor might not be sufficient.
What Is a DC Gear Motor and How Does It Differ?
A DC gear motor combines a standard DC motor with a gearbox attached to its output shaft. The gearbox consists of multiple gears that reduce the motor’s high-speed rotation to a slower speed while increasing torque. This mechanical advantage allows the motor to deliver higher torque at lower speeds, which standard DC motors alone cannot achieve efficiently.
The gearbox inside a DC gear motor is carefully designed to fit the motor’s characteristics and the application’s requirements. By changing the gear ratio, manufacturers like Kinmore Motor can provide customized solutions that optimize performance for specific tasks.
How Does the Gearbox Affect Performance?
The primary difference between a DC gear motor and a standard DC motor lies in the gearbox’s presence and function. The gearbox reduces the motor’s output speed by a specific ratio, often ranging from 5:1 to over 100:1, depending on the application. This reduction translates into:
- Increased torque: The motor generates more force to move heavier loads or overcome resistance.
- Reduced speed: The motor shaft rotates slower, offering better control for precise movements.
- Improved mechanical advantage: The motor can drive equipment that requires more power without increasing electrical input.
For example, if a standard DC motor spins at 3000 RPM, a DC gear motor with a 50:1 gearbox will reduce this speed to 60 RPM, increasing the torque proportionally.
Why Choose a DC Gear Motor Over a Standard DC Motor?
Choosing between a DC gear motor and a standard DC motor depends on your application’s requirements. Here are several reasons why you might opt for a DC gear motor:
- Higher Torque Needs: If your project requires strong force at low speeds—such as robotic arms, electric wheelchairs, or conveyor systems—a DC gear motor provides the necessary torque without compromising performance.
- Precise Speed Control: Gearboxes allow for finer speed control, essential for applications demanding accuracy, such as CNC machines or automated valves.
- Load Handling: DC gear motors can handle heavier loads than standard DC motors, thanks to the torque multiplication provided by the gearbox.
- Longer Motor Life: Operating at lower speeds reduces wear and tear on the motor, potentially extending its operational lifespan.
What Are the Common Applications for DC Gear Motors?
DC gear motors find their way into many industries because of their versatile capabilities. Some common applications include:
- Robotics: Providing controlled, powerful movements.
- Automotive: Powering window lifts, seat adjustments, and small drives.
- Industrial automation: Driving conveyor belts, packaging machinery, and assembly lines.
- Home appliances: Operating motorized blinds, electric locks, and pumps.
- Medical devices: Offering precise control in hospital beds and mobility aids.
Companies like Kinmore Motor specialize in manufacturing durable DC gear motors tailored for these industries, combining quality gearboxes with reliable motors to ensure optimal performance.
How Does the Gear Ratio Impact DC Gear Motor Performance?
The gear ratio is a crucial specification for any DC gear motor. It determines how much the speed is reduced and how much the torque is increased. Understanding this ratio helps you select the right motor for your needs:
- Low Gear Ratio (e.g., 5:1 to 10:1): Moderate speed reduction and torque increase. Suitable for applications needing some torque boost without a dramatic speed drop.
- Medium Gear Ratio (e.g., 20:1 to 50:1): Significant torque increase with reduced speed, ideal for medium load applications.
- High Gear Ratio (e.g., 100:1 and above): Large torque output at very low speeds, perfect for heavy-duty tasks.
Choosing the correct gear ratio is vital to balance speed and torque according to your project demands. Kinmore Motor provides detailed specifications and expert guidance to help customers pick the ideal gear ratio for their applications.
What Are the Efficiency Considerations Between the Two Motors?
Standard DC motors generally have higher efficiency at high speeds due to fewer mechanical components. However, when torque requirements increase, efficiency may drop as the motor strains. A DC gear motor, despite the mechanical losses in the gearbox (usually around 5-15%), can operate the motor at optimal speed while delivering high torque at the output shaft.
This results in overall better system efficiency, especially for applications requiring sustained torque over long periods. The tradeoff between slight gearbox losses and enhanced torque output often favors the DC gear motor in many industrial and commercial uses.
How Does Maintenance Differ Between a DC Gear Motor and a Standard DC Motor?
Standard DC motors are relatively low maintenance, requiring occasional brush replacement and cleaning. However, when adding a gearbox, the maintenance requirements can increase slightly due to the presence of moving gears:
- Gear lubrication: Periodic oiling or greasing of the gearbox may be necessary to reduce wear.
- Gear wear and tear: Over time, gears may need inspection for damage or replacement.
- Sealed gearboxes: Many DC gear motors use sealed or maintenance-free gearboxes to minimize upkeep.
Kinmore Motor offers a range of DC gear motors with sealed gearboxes designed for durability and reduced maintenance, making them a reliable choice for users seeking low upkeep without sacrificing performance.
Can a Standard DC Motor Be Converted Into a DC Gear Motor?
While technically possible, converting a standard DC motor into a DC gear motor involves attaching a compatible gearbox to the motor’s output shaft. This process requires careful alignment, selection of appropriate gearing ratios, and ensuring that the gearbox can handle the motor’s torque and speed.
For most users, purchasing a pre-assembled DC gear motor from a reputable manufacturer like Kinmore Motor is more practical. These integrated units undergo quality testing to guarantee performance and reliability, saving time and preventing potential mechanical failures.
What Should You Consider When Choosing Between a DC Gear Motor and a Standard DC Motor?
When deciding which motor to use, consider these key factors:
- Torque requirements: Do you need high torque at low speeds?
- Speed range: Does your application require precise speed control or high RPM?
- Load characteristics: How heavy or resistant is the load you want to move?
- Size and weight constraints: Can your design accommodate a gearbox?
- Maintenance preferences: Are you equipped to handle gearbox upkeep?
- Budget: DC gear motors often cost more but provide better performance for specific tasks.
By evaluating these criteria, you can make an informed choice that maximizes efficiency and reliability in your application.
Conclusion
Understanding the differences between a DC gear motor and a standard DC motor is vital for selecting the right motor for your needs. While standard DC motors excel at providing high speed with moderate torque, DC gear motors shine in applications demanding high torque at controlled, lower speeds. The addition of a gearbox transforms the motor’s capabilities, enabling powerful and precise performance.
Trusted brands like Kinmore Motor specialize in delivering quality DC gear motors that balance speed, torque, and durability for a wide range of industrial and commercial uses. Whether you need a motor for robotics, automation, or automotive systems, knowing these differences helps you choose the best solution confidently.