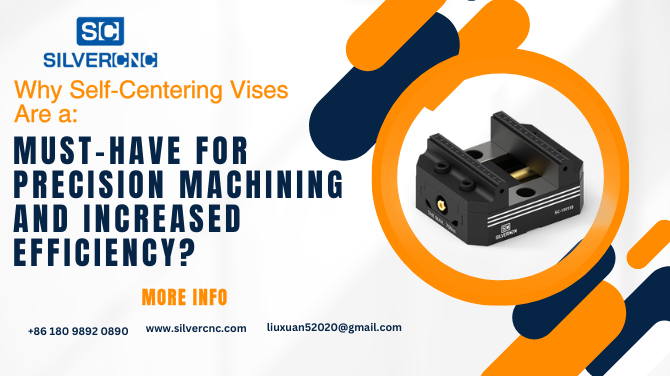
In the world of precision machining, where accuracy and efficiency are non-negotiable, every component and tool must contribute to the overall performance of the operation. One such tool that has proven to be invaluable in improving both accuracy and speed is the self-centering vise. Whether you’re in the automotive, aerospace, medical, or any other precision-driven industry, the self-centering vise is a key player in achieving the tight tolerances and repeatability that modern manufacturing demands.
But why exactly are self-centering vises so crucial for precision machining? How do they contribute to enhanced efficiency and improved product quality? In this article, we’ll explore the essential features of self-centering vises, their benefits, and why they have become a must-have tool for machinists who strive for perfection in every job. We’ll also take a closer look at how these vises can help your operations achieve faster turnaround times and more precise results, making them indispensable for any workshop focused on high-quality machining.
What is a Self-Centering Vise?
A self-centering vise is a tool used in machining operations to securely hold a workpiece while ensuring that it is precisely aligned at the center of the vise jaws. Unlike traditional manual vises, where the operator must adjust the workpiece by eye or with measuring tools to achieve proper alignment, a self-centering vise automatically centers the workpiece when the vise jaws are closed.
This feature eliminates the need for complex adjustments and allows the operator to position the workpiece quickly and accurately. The result is not only a secure hold but also a consistent, repeatable centering for multiple machining operations.
How Does a Self-Centering Vise Work?
A self-centering vise works based on a set of jaws that move inward symmetrically, ensuring that the workpiece is centered automatically. This is achieved through a mechanism that includes the following components:
- Fixed and Moving Jaws: The vise has a fixed jaw and one or more moving jaws. When the handle is turned, the moving jaws automatically move inward, centering the workpiece between them.
- Precision Mechanism: The mechanism within the vise ensures that both jaws move symmetrically, even if the workpiece is slightly off-center. This symmetry guarantees that the part is positioned exactly in the center of the vise with minimal operator intervention.
- Adjustable Clamping Force: Some self-centering vises come with adjustable clamping force, allowing operators to control the pressure applied to the workpiece. This ensures that delicate parts are held securely without the risk of deformation.
The beauty of the self-centering vise lies in its simplicity and effectiveness. By automatically centering the workpiece, machinists can focus on the machining process itself, reducing setup time and minimizing errors.
Key Benefits of Using a Self-Centering Vise
There are numerous reasons why self-centering vises are considered a must-have tool in modern machining. Below, we explore the top benefits that make these vises an essential part of any precision machining operation.
1. Improved Precision and Accuracy
Precision is the cornerstone of any machining operation. A self-centering vise ensures that the workpiece is always centered correctly within the vise, which leads to more consistent and accurate results. This level of accuracy is particularly important in industries that require tight tolerances, such as aerospace, medical, and automotive manufacturing.
The automatic centering feature eliminates the need for manual measurements or adjustments, which can often introduce errors. As a result, machinists can be confident that each part is positioned exactly as it should be, reducing the chances of costly mistakes and improving the overall quality of the final product.
2. Faster Setup Times
In traditional machining operations, setting up the workpiece can be a time-consuming process. The operator must manually adjust the workpiece and check its alignment to ensure that it’s centered properly. This setup process can take valuable time, especially when handling multiple parts or switching between different workpieces.
With a self-centering vise, setup times are drastically reduced. The vise automatically centers the workpiece when the jaws are closed, eliminating the need for time-consuming adjustments. This makes it easier for operators to move from one task to the next quickly, boosting overall productivity.
3. Consistency and Repeatability
Another significant advantage of self-centering vises is the consistency they provide. Once the vise is set up, it ensures that each workpiece is centered the same way, every time. This repeatability is crucial in high-volume production environments, where multiple parts need to be machined to identical specifications.
By reducing human error and eliminating manual adjustments, self-centering vises help maintain consistent positioning across all parts, ensuring that every component meets the required specifications. This repeatability also makes it easier to switch between different setups or batch jobs without worrying about misalignment.
4. Increased Efficiency
The efficiency of machining operations is significantly improved when using a self-centering vise. With automatic centering, operators can spend less time on setup and more time on actual machining. This not only speeds up the production process but also allows machinists to handle more workpieces within the same amount of time.
Additionally, because self-centering vises reduce the need for manual adjustments, there is less chance of errors that could lead to rework. Fewer mistakes mean less time spent fixing problems, which translates into higher overall efficiency.
5. Enhanced Clamping Force and Security
A self-centering vise offers secure and reliable clamping, which is essential for ensuring the stability of the workpiece during machining. Many vises provide adjustable clamping force, allowing operators to customize the pressure applied to the workpiece. This feature is particularly beneficial when working with delicate or irregularly shaped parts that require careful handling.
The enhanced clamping force of self-centering vises ensures that the workpiece is securely held in place throughout the entire machining process. This minimizes the risk of vibration, shifting, or damage to the part, leading to better results and fewer defects.
6. Versatility in Machining Operations
Self-centering vises are versatile tools that can handle a wide range of workpieces, from small precision parts to larger components. The ability to automatically center parts means that these vises can be used for various operations, including milling, drilling, and grinding.
Whether you’re working with round, square, or irregularly shaped parts, a self-centering vise can hold the workpiece securely and provide consistent results across different machining tasks. This versatility makes it an indispensable tool in any workshop.
7. Reduced Operator Fatigue
Machining can be physically demanding, particularly when operators are required to make constant adjustments or manually align parts. A self-centering vise minimizes the need for these manual interventions, reducing the physical strain on operators.
By automating the centering process, operators can focus on more critical tasks, allowing them to work more efficiently and with less fatigue. This leads to improved safety as well as better morale among the workforce.
8. Improved Safety
When workpieces are not securely held in place, they can shift or move during machining, leading to potential accidents or damage to both the part and the machine. Self-centering vises are designed to hold the workpiece securely and prevent movement, reducing the risk of accidents.
By ensuring that parts are clamped and aligned properly, self-centering vises contribute to a safer working environment for machinists. This added security not only protects workers but also helps avoid costly machine damage.
9. Cost-Effectiveness in the Long Run
While the initial investment in a self-centering vise may be higher than traditional vises, the long-term cost savings are significant. The increased precision, faster setup times, and improved efficiency contribute to overall cost reduction in machining operations.
Additionally, the reduction in errors and rework means that less material is wasted, further cutting costs. When you consider the enhanced productivity and repeatability, the self-centering vise is a cost-effective solution that offers substantial returns on investment.
Applications of Self-Centering Vises
Self-centering vises are widely used in a variety of machining operations, especially where high precision is required. Some of the most common applications include:
- Aerospace Manufacturing: For machining components such as turbine blades, engine parts, and structural components with tight tolerances.
Automotive: For producing parts such as engine blocks, gears, and transmission components. - Medical Device Manufacturing: To machine critical components like surgical tools, implants, and diagnostic devices.
Toolmaking: For precise manufacturing of molds, dies, and tooling.
Conclusion: Why Every Machinist Needs a Self-Centering Vise
In conclusion, a self-centering vise is an essential tool for anyone involved in precision machining. Its ability to automatically center the workpiece, increase efficiency, reduce setup times, and ensure repeatable accuracy makes it a must-have for any machining operation focused on producing high-quality parts.
Whether you’re working in high-volume production or low-volume, high-precision machining, the self-centering vise provides the accuracy, consistency, and reliability needed to meet the demands of modern manufacturing. By reducing human error, improving clamping security, and offering greater versatility, the self-centering vise is an investment that will pay off in improved productivity, reduced costs, and superior product quality.