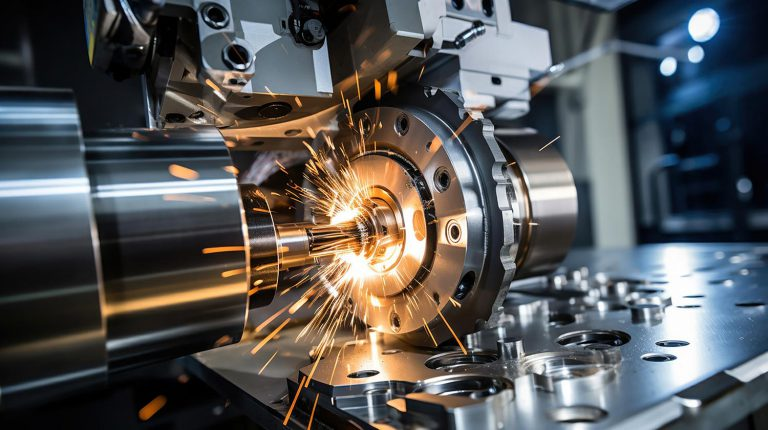
Grade Specifications of Free Cutting Steel
Commonly Used Free Cutting Steel Grades
Free cutting steel, also known as machinable steel, is specifically engineered to enhance machinability through the addition of elements like sulfur, phosphorus, and lead. These elements play a crucial role in defining the grade specifications of free cutting steel.
Chemical Composition and Mechanical Properties
The chemical composition of free cutting steel is tailored to improve its machinability. Sulfur forms manganese sulfide (MnS) inclusions, aiding in chip formation and breaking, which reduces the contact area between the tool and the workpiece. This results in smoother machining operations and longer tool life. Lead exists in the steel as fine particles that melt during cutting, acting as a lubricant to reduce friction and tool wear. Furthermore, phosphorus dissolves in ferrite, increasing hardness and strength, and making chips easier to break.
The mechanical properties of free cutting steel grades are influenced by these elements, providing enhanced machinability while maintaining adequate strength for various applications. However, excessive sulfur can negatively impact mechanical properties by reducing ductility.
Applications and Suitability for Different Industries
Free cutting steel grades are extensively used in industries that require precision mechanical parts with high levels of automation and accuracy. The automotive industry benefits from these steels for manufacturing components like gears and shafts due to their excellent machinability. Similarly, the electronics industry utilizes free cutting steel for producing intricate parts with high surface finish requirements.
Standards and Classifications in Various Regions
Different regions have established standards and classifications for free cutting steel grades to ensure consistency in quality and performance. These standards outline the permissible chemical compositions and mechanical properties that define each grade. For instance, sulfur-free-cutting steel improves machinability through manganese sulfide formation, while lead free-cutting steel provides lubrication during cutting without affecting the steel’s mechanical properties at room temperature.
Advantages and Limitations of Free Cutting Steel Grades
Benefits of Machining Processes
Improved Machinability and Surface Finish
Steel grades that are classified as free cutting provide advantages in machining operations as they exhibit superior machinability qualities. Ranked highly for machinability reasons. Cutting steel enhances efficiency in production by minimizing tool wear and extending the lifespan of tools. This results in enhanced surface finishes for machined parts that’re ideal for applications where appearance plays a crucial role.
Cost Efficiency in Production
The use of free cutting steel grades contributes to cost efficiency in production by reducing machining time and minimizing tool wear. The reduced friction during machining processes allows for faster cutting speeds, resulting in increased productivity.
Potential Drawbacks and Considerations
Impact on Material Strength and Durability
While free cutting steels provide excellent machinability, there are potential drawbacks regarding material strength and durability. The presence of elements like sulfur can lead to reduced ductility, which may impact the overall toughness of the material under certain conditions.
Environmental and Safety Concerns
Environmental compliance is an essential consideration when using free cutting steels. Environmental Compliance: This steel complies with EU SGS environmental certification standards, making it suitable for export in various mechanical equipment. However, certain elements used to enhance machinability may raise environmental concerns if not properly managed during production or disposal.
In summary, understanding the grade specifications of free cutting steel is essential for engineers seeking materials that balance machinability with mechanical performance. By carefully selecting appropriate grades based on application requirements and regional standards, engineers can optimize their designs for efficiency and cost-effectiveness while considering potential limitations related to strength and environmental factors.
Selection Criteria for Engineers
Factors Influencing Grade Selection
Choosing the right free cutting steel grade is critical for engineers to ensure optimal performance and cost-effectiveness in their projects. Several factors influence the selection of free cutting steel grades:
Project Requirements and Specifications
When engineers choose a type of free cutting steel for their projects, they need to consider the specific requirements and details involved, such as properties like tensile strength and hardness, as well as factors like machinability and surface finish quality. The presence of elements such as sulfur and lead in free cutting steel can improve machinability, might have an impact on other properties too. For instance, sulfur helps create sulfide (MnS) inclusions which assist in chip formation and breaking down material during machining by reducing the contact area between the tool and workpiece. This feature is advantageous for tasks that demand machining skills.
Compatibility with Other Materials
The compatibility of free cutting steel with other materials used in a project is another crucial factor to consider. Engineers should evaluate how the selected grade interacts with different materials to avoid issues such as galvanic corrosion or adverse chemical reactions. Lead exists in the steel as fine particles that melt during cutting, acting as a lubricant to reduce friction and tool wear, which can be advantageous when working with materials that are prone to friction-induced damage.
Tips for Optimal Grade Utilization
To make the most of free cutting steel grades, engineers can follow these tips for optimal utilization:
1. Understand Material Properties: Thoroughly analyze the chemical composition and mechanical properties of the chosen grade to ensure it meets project specifications.
2. Select Appropriate Machining Techniques: Use machining techniques that complement the properties of free cutting steel, such as high-speed machining or precision turning.
3. Consider Environmental Impact: Ensure compliance with environmental regulations by selecting grades that meet standards like EU SGS certification. Environmental Compliance: This steel complies with EU SGS environmental certification standards, making it suitable for export in various mechanical equipment.
Promispecial®: Enhancing Performance with Advanced Free Cutting Steel Products
Promispecial® is at the forefront of innovation in the field of tailored free cutting steel solutions, offering advanced solutions that enhance performance across various applications. By leveraging state-of-the-art production processes and material compositions, Promispecial® delivers products that meet stringent industry demands.
Promispecial®’s range of free cutting steels incorporates elements such as sulfur, phosphorus, lead, calcium, selenium, tellurium, and bismuth to optimize machinability without compromising on quality. Calcium helps form a thin oxide film that reduces friction and prevents tool wear during cutting, providing an edge in high-speed machining environments.
Through its commitment to innovation and quality assurance at every stage—from raw material selection through final finishing—Promispecial® provides engineers with industry-specific applications for their complex engineering challenges involving free cutting steels.