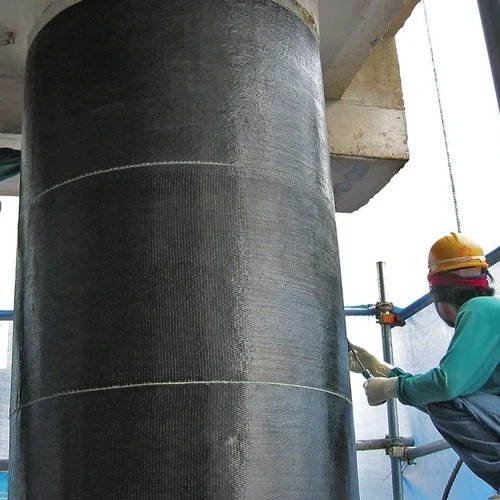
Structural deterioration in concrete slabs is a growing concern across India. Buildings are aging. Loads are increasing. And environmental damage is taking its toll. As property owners and engineers seek safer, long-term solutions, one method is gaining popularity. That method is Carbon Wrapping for Slabs. It delivers enhanced strength without complete reconstruction.
Understanding the Problem of Slab Weakness
Slabs are susceptible to cracking over time. These result from overload, bad building techniques, or corrosion. The safety of people is at risk due to weak slabs. They also lessen the structure’s usefulness. Many constructions in India last longer than planned. Rebuilding them, however, is expensive. Many turn instead to structural retrofitting because of this. This is the point at which Carbon Wrapping for Slabs becomes useful.
What Is Carbon Wrapping?
Carbon fiber reinforced polymer (CFRP) sheets are used in carbon wrapping. These are adhered to the surfaces of the structure. The technique is corrosion-resistant, strong, and lightweight. It was first employed in aerospace and is currently being used in infrastructure. Without significantly increasing the slab’s weight, carbon wrapping for slabs strengthens it. Therefore, it doesn’t put further strain on foundations.
Why Indian Buildings Need Retrofitting
India’s urbanization rate is rising quickly. This increases the need for long-lasting structures. Many older structures, however, are not earthquake-resistant. Concrete is also harmed by pollutants, heat, and heavy rains. Performance can be restored in these situations with Carbon Wrapping for Slabs. Additionally, it prevents the disturbances that complete deconstruction could bring about. Above all, it promotes sustainability.
Benefits of Carbon Wrapping for Slabs
There are several advantages. The application is quick, to start. In both household and commercial settings, this reduces downtime. Secondly, its strength-to-weight ratio is high. This implies that you receive excellent help without being overloaded. Thirdly, it makes things more durable. Structures become more impervious to additional moisture or cracking. Finally, the load capacity is increased by carbon wrapping slabs. This is essential for areas that now accommodate more people or larger gear.
Applications in the Indian Context
In India, slab retrofitting is crucial for infrastructure. It is used in workplaces, schools, hospitals, and historic apartments. Vertical expansions are also typical in many metropolitan areas. Slabs need to be upgraded first. For slabs, carbon wrapping is the best option. It can be used on precast buildings as well as suspended and cantilever slabs. Additionally, it works well in areas like Gujarat or Northeast India that are prone to earthquakes.
Step-by-Step Process of Carbon Wrapping
Surface preparation is the first step in the procedure. Old paint, oil, and dust are eliminated. The structural fissures are then fixed. After that, sticky resin and primer are applied. Sheets of carbon fiber are carefully positioned. To eliminate air pockets, they are compressed. Lastly, a layer of protection is applied. The slab gets significantly stronger with the right curing. These measures must be followed by certified professionals. This guarantees the safety and efficacy of carbon wrapping for slabs.
Safety Considerations and Guidelines
When retrofitting, safety always comes first. Therefore, it’s crucial to use carbon fiber sheets that have been tested for quality. They have to adhere to global norms. Specific guidelines are also provided by building codes in India. Engineers must assess both the intended strength gain and the current load. A thorough structural audit should always include carbon wrapping for slabs. Only skilled applicators ought to do the job. This reduces risk and guarantees enduring outcomes.
Cost Factors and Long-Term Value
The long-term worth is substantial, even though the initial cost could appear costly. Future repairs are less necessary when slabs are carbon-wrapped. It adds years to the structure’s lifespan. Heavy equipment is not required. Compared to reconstruction, labour expenses are cheaper. Avoiding downtime is essential in India, where a large number of properties generate revenue. As a result, the approach ultimately saves money and time.
Comparison With Other Strengthening Techniques
Other techniques include external bracing, jacketing, and steel plating. But these frequently increase dead load. Additionally, they might alter the building’s appearance. Carbon Wrapping for Slabs, on the other hand, is elegant and doesn’t need any structural changes. It doesn’t encroach. It is therefore ideal for usage in historic or occupied structures. In contrast to steel-based substitutes, carbon fibers are also resistant to rust.
Who Should Consider Carbon Wrapping?
Older building owners ought to look into this option. Institutions that intend to grow should do the same. Additionally advantageous are property managers who wish to prevent service interruptions. It is also helpful to engineers working on seismic enhancements. Slab carbon wrapping provides a rapid, hygienic, and effective solution. It is perfect for public infrastructure as well as private residences, businesses, hospitals, and factories.
Real-Life Use Cases
Builders have successfully applied this technique in a number of Indian metropolises. For instance, carbon fiber covers have been employed in aged hospitals to comply with safety regulations. In a similar vein, classroom slabs in historic school buildings were reinforced for increased safety. This approach was also utilized to restore parking lots with cracked slabs. These illustrations demonstrate the dependability and adaptability of carbon wrapping for slabs.
Building safety and resilience becomes essential as India continues to urbanize. Time, money, and the environment are all saved when repairs are made instead of rebuilds. Slab carbon wrapping is a cutting-edge, practical retrofit option. It works well with a variety of Indian structures. This approach offers significant advantages for longevity, load improvements, and safety. When used properly, it prolongs a structure’s lifespan and provides years of peace of mind.